Top power supply PCB assembly guidelines!
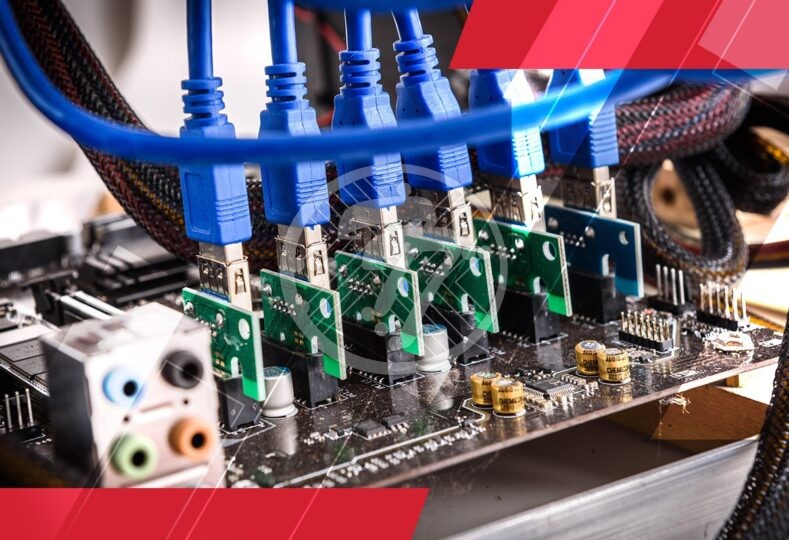
All PCB boards need electrical power; however the need isn’t just for more power but also clean power. That is something that is made possible by a successful PCB board design. With the right PCB design, clean, uninterrupted power can be provided to the circuitry. It is also important to remember that electrical power will generate heat & the heat, in turn, will impact the circuit board. A number of aspects therefore need to be kept in mind.
Before we look at some of the considerations that will lead to a cleaner power supply, it will be worthwhile to look at the kind of power supply available.
Broadly, power supplies are broken up into two main groups:
- Linear power supplies are typically used in systems where the power requirements are lower.
- SMPS or Switch-mode power supplies are more complex as also more efficient. The thing to remember is that their switching noise can lead to EMI. SMPs, in turn, may be isolated or non-isolated. Non-isolated SMPs are further of the following types:
- Buck – It steps down the voltage while the current is stepped up
- Boost – It steps up the voltage while stepping down the current
- Buck-Boost – It has elements of both & can step up or step down the voltage.
It is important to remember that since you will deal with high levels of current, the trace widths need to be adequate. Additionally, in order to control the noise, it is important to ensure that the component placement is optimized as the routing is short. Also the design needs to ensure effective heat dissipation. Let us look at some of the guidelines to be followed in detail:
PCB Power Supply Guidelines to follow:
- When you are dealing with a multi-layered board, it is important to have the ground or power plane between the outer layer with the power supply components & the inner layer with sensitive signals. The ground plane offers electromagnetic shielding. In case it is not possible to devote a layer, a ground polygon is ideal. If you do go in for a ground plane, it is essential that the PCB power supply design is separated from the common ground. Also the connection between the two grounds should be limited to one point on the board. In the absence of this, you run the risk of ground loops.
- It is imperative to keep the power supply parts close together so that the trace lengths are minimized. This will help to reduce any resistive losses as well as electromagnetic noise emissions. Where possible the use of polygon pours is recommended.
- In terms of component placement, it is also important to separate heat-generating components from heat-sensitive components. Also using copper will ensure that heat is distributed from the hotspots and that thermal issues aren’t exacerbated. If you are dealing with a buck converter the input capacitor should be kept next to the IC. As for the output capacitor, it should be placed immediately after the conductor.
- Speaking of heat dissipation, it is important to include proper cooling methods such as heat sinks, fans, thermostatic coolers & more. Heat sinks are, however, best used with a linear regulator.
- As for the routing, it needs to have short, direct traces. As far as possible blind and buried vias need to be avoided as they add to the inductance.
To Sum Up
The above best practices will ensure that your PCB power supply is optimized. However, a key area remains, which is having the boards manufactured & assembled to these exact details. Choosing the right electronic contract manufacturer who can manufacture & assemble your boards as per these best practices is therefore essential. Among other things since the PCB requires tight placement, you need an experienced assembler who can take care of all the requirements. Typically, the manufacturer & the assembler need to be able to work with you at the design stage itself so that there are no manufacturability issues at a later date. An experienced manufacturer & assembler is also equipped with all the industry best practices that make sure that you do not need to reinvent the wheel or waste precious time, especially since quick time-to-market is a key competitive advantage in today’s times.
At Technotronix, we are fully equipped to handle your PCB manufacturing requirements. We follow industry best practices to ensure we deliver cutting-edge products. Our team of experts and state-of-the-art manufacturing facility ensures that all our PCBs meet the industry standards of quality and testing.
If you have any questions or any requirements related to PCB assembly, please feel free to contact us via email at [email protected] or call 714/630-9200.