How to find the Perfect Electronic Assembly Company for your Industry?
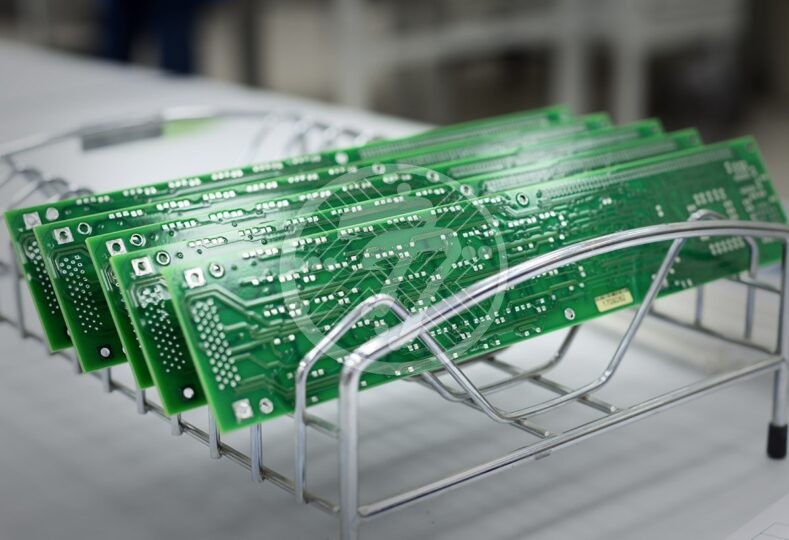
The choice of the right electronics assembly company is one of the most crucial decisions that you can take when it comes to the success or failure of your electronic product. Taking the time to get a comprehensive understanding of the company and its competencies can go a long way in saving you precious time later.
Here is a handy guide on the factors to look for in making your choice:
Experience of the Electronic Assembly Company
With miniaturization of devices, PCBs are becoming increasingly complex. To this end, you need a manufacturer who has the requisite experience. Such manufacturers will be armed with a huge body of industry best practices that will ensure that you do not have to reinvent the wheel. Some of the areas to probe include:
- How many years have they spent in the business?
- What kind of expertise do their professionals have?
- Whether the manufacturer has experience with surface-mount technology or with through-hole manufacturing or both.
- What kind of products have they handled in the past? Which industries have they dealt with?
- What kind of production volumes can they deal with?
Electronic Assembly Quality
You certainly want a manufacturer who gave give you high quality PCB assembly. To evaluate this, involves checking for a number of factors:
- Does the company have state-of-the-art equipment?
- Do they have industry leading certifications?
- What kind of client testimonials do they have? You could even reach out to their clients to evaluate how satisfied they are.
Testing Protocols for Electronic Assembly
Robust testing protocols are what stands between you and a quality product. You need to therefore ascertain the kind of testing procedures the company follows. Automated Optical Inspections, component level checks and in-circuit verification are some of the things to look for. In the absence of these you could contend with costly errors that could even lead to product recalls and cost the company its reputation.
Customer Support at Electronic Assembly Company
Prompt customer support is not just a nice to have feature when it comes to a crucial component like a PCB. You certainly want a manufacturer that can answer your questions and offer proactive solutions. Speaking to the customer support representative and finding out what kind of turnaround times they offer, whether they can customize solutions for you, are all good indicators.
Electronic Assembly Cost
Last but definitely not the least, you want to go with a manufacturer that offers optimal costs. It is important, however, to remember that costs are a function of a number of factors including but not limited to:
- The quantity required
- The complexity of the product
- Shipping costs, and more
Costs however cannot be the sole determinant of your decision as you do not want to chase low costs alone at the expense of quality.
Besides delving into each of the above factors in detail, it will be good to watch out for the following red flags. If you do see them appear, it is a good enough indicator of the fact that the manufacturer may not be the right fit for you:
- Delay in responding. If you see that your queries aren’t being promptly and suitably addressed, you sure want to give the company a miss. After all, you do not want to be in a situation where you need to follow up on your project without receiving any satisfactory answers.
- Inability to understand your bespoke requirements. If the manufacturer does not show flexibility in going all out and understanding your bespoke requirements to be able to deliver customized products, this is yet another red flag.
- Inability to provide references. Now this means that the company isn’t confident of its capabilities and of its clients to express their satisfaction in their services. A definite no-no.
- Prohibitive costs. If the quote received from the manufacturer is prohibitively high and there are no explanations to go with it, you may want to re think your decision.
Go ahead and choose the right PCB Assembly partner that can do justice to your project and become a partner in the competitive advantage you bring to the table. Get the best PCB Industrial Solutions from us.
Looking for an electronic assembly company? At Technotronix, we have over 40 years of experience in fabricating and assembling high quality PCBs. You can count on us for high quality PCBs, no matter what the level of complexity. With the demand for consumer electronics growing exponentially, what is also growing is the demand for quality electronics PCB assembly. Well designed and assembled electronics circuit boards are the mainstay of the consumer electronics industry.