How to Speed Up the PCB Production Time Using SMT PCBs?
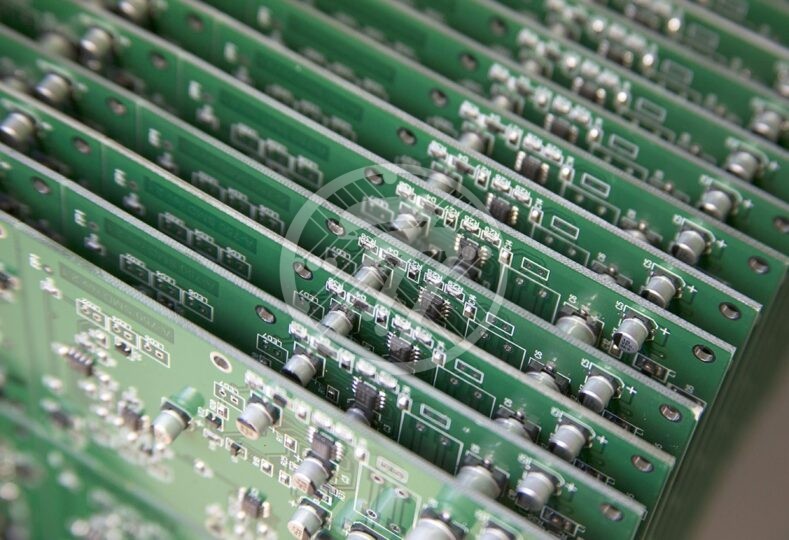
A large percentage of today’s mass-produced electronics hardware is manufactured using Surface Mount Technology or SMT as it is popularly known as. Not without reason! SMT PCBS go a long way in speeding up PCB Production time besides offering a host of other advantages.
Surface Mount Technology for High Speed PCB Production:
Essentially Surface mount technology (SMT) took the basic concept of through-hole manufacturing and went on to offer a major improvement. With the use of Surface Mount Technology, PCBs do not need to have holes drilled through them. Instead what they do is to make use of solder paste. This phenomenally simplified the process besides adding a lot of speed. While it is true that SMT mount components may not have the strength that a through-hole mount may have but they offer a whole lot of other advantages that offset this issue.
Surface Mount Technology goes through a 5-step process as below:
1. Production of PCB- this is a stage where the PCB is actually produced with solder points
2. Solder is deposited onto the pads that allows components to be fixed to the board
3. With the help of machines components are placed at the precise solder points
4. The PCBs are baked in order that the solder is hardened
5. The finished assemblies are inspected
What makes SMTs different from Through Hole include:
- The issue of space that widely occurs with through-hole mounting is resolved by the use of Surface Mount Technology. SMT also offers design flexibility as it offers PCB designers a free rein to create specialized circuits. Reduced component size means that more components can be accommodated on a single board and fewer boards are required.
- Components in SMT mounting are leadless. Shorter lead lengths of Surface Mount Components reduce propagation delays as well as package noise.
- There is higher component density per unit area as it allows components to be mounted on both sides
- It is suitable for high volume production which in turn leads to lower costs
- Reduced size leads to higher circuit speed. This in fact is one of the is one of the main reasons most manufacturers opt for this method.
- The surface tension of the molten solder pulls components into alignment with solder pads. This in turn automatically corrects any small errors that may have occurred in component placement.
- SMT has proven to be more stable in conditions where there is a lot of vibration or shaking.
- SMT parts are often less costly than comparable through-hole parts.
Importantly, SMT allows for a far lower production time as no holes are required to be drilled. Also, SMT components can be placed at rates of thousands of placements per hour, as against less than a thousand for through hole mounting. This in turn leads to the product being manufactured as quickly as it is envisaged which further leads to reduced time to market. If you are therefore looking at speeding up PCB Production time, SMT is clearly the answer. With the use of Design for Manufacturing (DFM) software tools, the need for rework and redesign of complex circuits is significantly reduced, further adding to the speed as well as the possibility of complex designs. Check out the guide on why is process control measurement essential to stop defects in SMT PCB Assembly.
All this is not to imply that SMT does not come with its own inherent disadvantages. SMT can be unreliable when it is used as the only attachment method for components that face a whole lot of mechanical stress. Components that generate a lot of heat or bear a high electrical load cannot be mounted using SMT. This is because the solder can melt under high heat. Through-hole Mounting, therefore is likely to be continued to use in cases where there are special mechanical, electrical and thermal considerations that make SMT ineffective. Also SMT isn’t suitable for prototyping as there could be need to add or replace components at the prototyping stage, which a high component density board may find hard to support.
Use of Surface Mounted Technology
With the formidable advantages offered by SMT, little surprise then that they have taken over as the main design and fabrication standard today. Essentially they are used in any situation that calls for production of highly reliable and high volume PCBs.
At Technotronix, we are fully equipped to handle your SMT Manufacturing requirements. With over 4 decades of experience in PCB manufacturing as well as assembling PCBs with differing levels of complexities, we follow industry best practices to ensure we deliver cutting-edge products. Our team of experts and state-of-the-art equipment ensures that all our PCBs meet the industry standards of quality and testing. It is our vast portfolio of satisfied clients that stand as the biggest testimony to our success. In case if you have any questions, please feel free to contact us via email at [email protected]