5 Effective Ways of Digital Image Correlation benefits in Lead-free PCB Manufacturing
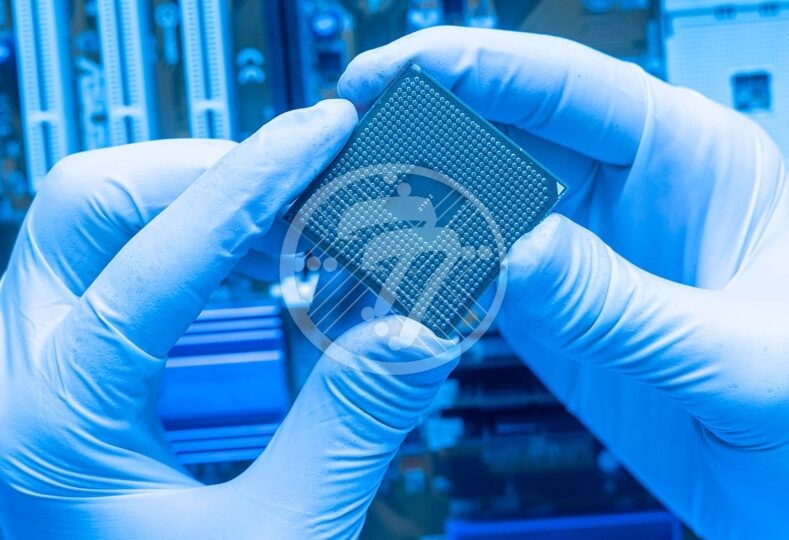
When it comes to manufacturing PCB manufacturing, reliability is a very important issue. The approach that works best is to proactively design it for reliability, instead of hoping that it works well, retrospectively. A whole lot of factors go into Making for reliability; a lot of it has to do with understanding how materials behave as well as interact with each other during the operational process. It is therefore important to study material characteristics such as Coefficient of Thermal Expansion or Transition Temperature. Selecting the wrong material can have a number of implications including but not limited to stress on the components and the joints.
An extremely useful tool to enable the process of reliability is Digital Image Correlation or DIC, as it is commonly referred to.
What this technique essentially does is that it proactively measures properties and provides a reliable value. So whether it is selection of material or test monitoring or simulation, you can be sure that you cannot go wrong! Digital Image Correlation or DIC is basically an optical method that can measure both displacements and deformation. In this method specimens are created with a contrasting speckle pattern. The specimen can then be tracked to see how it deforms. The advantage that it offers is that contact with the specimen is therefore not required. Also, DIC is able to produce full field displacement, which is not possible in other methods. DIC can also be performed with just a single camera. However in case if out of plane measurements are required, it needs multiple cameras. It can also be performed irrespective of the specimen size.
The technique has been growing in popularity in a whole lot of mechanical testing applications as it is easy to use. With computer technology and digital cameras showing a whole lot of technological advancements, the use of DIC is only slated to grow. DIC is therefore being extended to any imaging technology. It particularly finds a lot of use when it comes to Lead free PCB Manufacturing.
5 Reasons Why Digital Image Correlation is beneficial for Lead Free PCB:
1. Material properties
– DIC can be used to describe a whole lot of material properties like:
- Young’s Modulus
- Poisson’s Ratio
- Coefficient of Thermal Expansion and more
It thus helps arrive at the best material to be used in case of PCB laminates. It can also help identify solder fatigue risks.
2. Test Monitoring
– Digital Image Correlation helps to study displacement and strain measurements. It can help monitor elements such as tensile and bending testing among others.
3. Warpage
– Often during reflow soldering, warpage is a concern. If there is a lot of warpage there are multiple issues such as interconnect formation, solder joint bridging and even the fear of component cracking. DIC can help identify the warpage and thus add to the reliability.
4. Finite Element Analysis (FEA)
– Through the use of DIC both input material properties as well as simulation results can be tested. Complex assemblies often see problematic strain regions. With FEA results this problem is significantly reduced.
5. Dynamic Applications
– Besides being used in static applications, DIC can also be used in dynamic applications such as vibration testing.
The benefits of DIC in lead free PCB manufacturing therefore cannot be over emphasized. With the use of this technique you can also rest assured that the PCB thus manufactured will live up to its reliability benchmarks.
Technotronix is one of the leading provider of Lead Free PCB manufacturing services to all the dominant industries. Having a strong manufacturing unit with a strong tool room and a team of experts, we are able to keep quality at the nucleus in each stage of PCB manufacturing. To get proper consultation or share your requirements to get a perfect PCB with cost effective strategy or to get a quote, drop an email to [email protected] or give a call @ 714/630-9200!