What is the role of UPS PCBs in data centers, hospitals, and industrial automation?
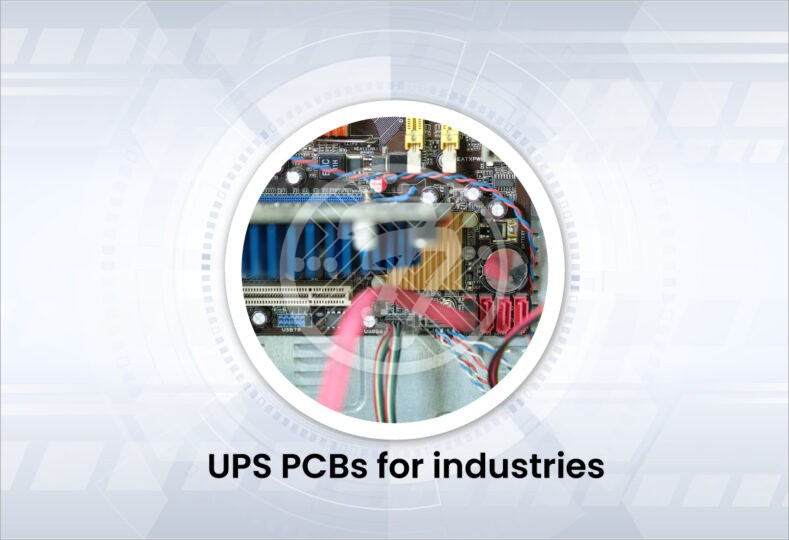
In a world that thrives on uninterrupted connectivity, consistent power is more than convenience—it’s a lifeline. From the relentless demands of data centers to the life-critical operations of hospitals and the precision-driven realm of industrial automation, power reliability is non-negotiable. At the center of this reliability is the Uninterruptible Power Supply (UPS)—and more specifically, the Printed Circuit Boards (PCBs) within these systems that quietly manage, control, and safeguard the flow of electricity.
UPS PCBs might not get the spotlight, but they are the brains behind every successful power backup operation. Whether its keeping servers running during a blackout, powering surgical equipment during an outage, or ensuring production lines never falter, UPS PCBs are the unsung heroes of modern infrastructure. This blog explores their roles in detail and shows why they matter so much in high-stakes environments.
1. Understanding UPS and their PCBs
A UPS provides backup power during interruptions—ranging from milliseconds-long brownouts to full blackouts. Most modern UPS systems—especially those used in critical industrial applications—are online for double-conversion designs. In these, incoming AC power is rectified to DC, charges the battery, and then inverted back to clean AC for the load.
At the core of these functions are specialized PCBs, responsible for:
- Rectifier boards that control AC-to-DC conversion.
- Inverter boards that transform battery power back into AC.
- Control logic boards that manage transitions, monitor load, and communicate status.
- Power conditioning modules provide voltage regulation and surge protection.
High-quality PCBs ensure stable power transformation, efficient operation, and systems that meet uptime requirements—even during complex failure scenarios.
2. Role in Data Centers
a. Ensuring Zero-Downtime Operations
Data centers demand constant power – any interruption risks lost data, hardware damage, or downtime costing thousands per minute. UPS PCBs enable:
- Continuous power quality management, smoothing voltage fluctuations, and preventing transient damage.
- Instantaneous transfer to battery power during outages, facilitated by controlling PCBs coordinating rectifiers, inverters, and static bypass switches.
- Support for scalable, modular systems (e.g. N+1 redundancy). PCBs enable hot-swappable and parallel configurations to maintain uptime during expansion or maintenance.
b. Advanced Grid Services
Beyond backup, UPS systems can actively support the power grid using advanced features programmed into their PCBs:
- Demand response—shifting load from grid to batteries during peak demand.
- Grid frequency regulation—absorbing or injecting power to stabilize 60 Hz fluctuations.
- Energy arbitrage—storing electricity when cheap and feeding it back when rates are high.
These functions rely on embedded firmware and sophisticated control algorithms on PCBs—transforming UPS units from passive backups into active grid assets.
3. Hospitals: Power Protection with Patient Safety in Mind
In healthcare settings, power reliability correlates directly to patient lives—making UPS systems critical, and their PCBs even more so.
a. Safe Handover to Life-Saving Systems
Hospital UPS units maintain power to:
- Life-support machines, imaging systems, and ventilators.
- Critical monitoring and safety equipment during generator transitions
Control PCBs ensure zero-break transitions, prevent electrosurgical noise, and maintain clean voltage for sensitive medical instruments.
b. Rigorous Safety and Compliance
Hospital-grade UPS PCBs include:
- Redundant protection circuits to prevent single-point failures.
- Isolation and EMC filters to reduce electrical interference with medical devices.
- Monitoring and alarms tied into building systems to swiftly report faults.
PCB-level reliability and regulatory certification underlie hospital safety systems—critical in emergencies.
4. Industrial Automation: Reliable Power for Production
In industrial environments, automation lines and control systems cannot tolerate power fluctuation or failure.
a. Protecting Control Systems
UPS systems keep PLCs, HMIs, and automated lines powered during brownouts or outages. PCB functions include:
- Power smoothing and voltage control to prevent malfunctions or resets.
- Fast transfer to stored power to maintain production flow.
- Pre-shutdown routines allowing controlled halting of motors and robots.
b. Onsite Conditioning and Control
Industrial-grade UPS PCBs often integrate:
- EMI/RFI filtering to handle noisy industrial power lines.
- Programmable signal interfaces for SCADA/BMS integration.
- Robust certifications to endure heat, dust, and vibration common in manufacturing spaces.
c. Maintenance and Decommission Management
These PCBs provide:
- Diagnostic modules that identify battery degradation or board faults.
- Modular designs enabling field replacement and minimal downtime.
5. Shared Benefits Across Applications
While the environments differ, UPS PCBs provide critical capabilities across all sectors:
- Power Conditioning: Rectifier/inverter boards clean and maintain voltage quality.
- Seamless Switching: Static bypass and smart control logic eliminate delays.
- Battery Management: PCBs manage charging, discharge control, and health monitoring.
- Redundancy & Scalability: Modular PCBs support hot-swappable units and parallel operations.
- Diagnostics & Maintenance: Embedded sensors and alert systems preempt failures.
- Grid Integration: Firmware enables UPS systems to act as grid assets.
- Safety & Compliance: Isolation, filtering, and fail-safes ensure regulatory standards are met.
6. The Future: Smarter, Leaner, More Capable PCBs
As technology evolves, key trends in UPS PCB design include:
- Lithium-ion battery support, offering faster recharge cycles and higher energy density
- IoT-enabled monitoring, with remote alerts, analytics, and firmware updates.
- More compact designs using high-power-density components and optimized thermal layouts.
- Sustainable energy use, enabling microgrid and renewable integration via PCB control systems.
These advances promise UPS units that are smarter, greener, and more responsive.
Conclusion
In mission-critical environments, there is no room for error when it comes to power supply. UPS PCBs are not just components—they are the backbone of intelligent, resilient, and responsive backup power systems. Their design and functionality are the reasons hospitals continue surgery during blackouts; data centers avoid catastrophic downtime, and industrial lines maintain continuous production even when the grid falters.
As industries evolve and demand smarter, more efficient energy solutions, the role of UPS PCBs will only grow more vital. They’re becoming more compact, intelligent, and capable of integrating with modern digital ecosystems. Whether you’re responsible for IT uptime, patient safety, or manufacturing efficiency, understanding the importance of UPS PCBs means being a step ahead in securing uninterrupted performance.
Reliable power begins with smart design—and that design starts with a UPS PCB.
Looking to enhance the reliability and performance of your UPS systems? We deliver high-quality, custom UPS printed circuit board manufacturing to meet the critical demands of data centers, hospitals, and industrial automation environments. Reach out [email protected] today to discuss your project needs and discover how our advanced PCB solutions can support uninterrupted power and operational efficiency where it matters most.