Why do Automotive PCBs require special fabrication techniques for high-temperature environments?
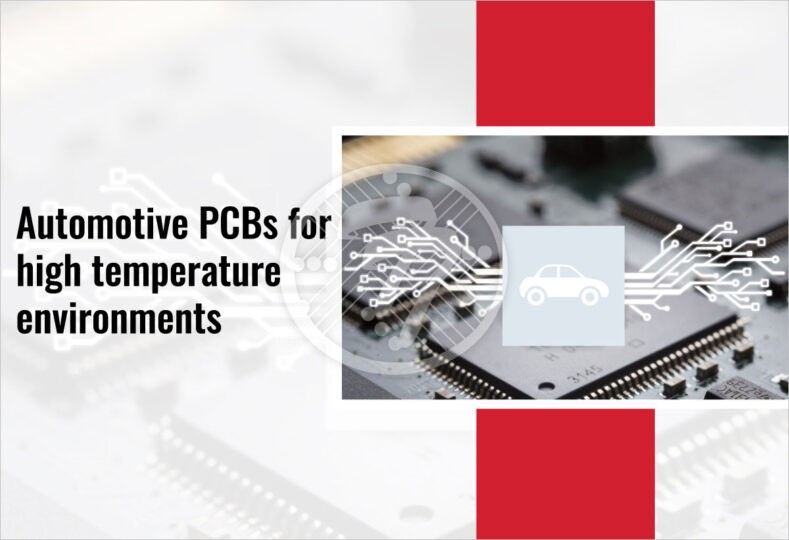
Printed circuit boards (PCBs) play a critical role in modern automotive electronics. From engine control units to infotainment systems and advanced driver-assistance systems (ADAS), PCBs form the backbone of automotive electronic components. Unlike consumer electronics, automotive applications often operate in extreme temperature environments, which places unique demands on PCB materials, design, and fabrication processes. In this article, we explore why automotive PCBs require special fabrication techniques for high-temperature environments, the challenges they face, and the solutions used by engineers and manufacturers.
Importance of Automotive PCBs
Automotive PCBs are essential in enabling various vehicle functions, such as:
- Powertrain control (ECU, transmission control)
- Lighting systems (LED drivers, adaptive lighting)
- Safety systems (airbags, ABS)
- Navigation and entertainment (GPS, touchscreen displays)
- Advanced Driver-Assistance Systems (ADAS)
These applications require reliable and durable PCBs that can operate effectively in varying and often harsh environmental conditions, including elevated temperatures, mechanical vibrations, and chemical exposure.
Why are high temperatures a concern in automotive electronics?
Automobiles experience a wide range of operating temperatures. Under-the-hood applications, in particular, are prone to extreme heat.
For example:
- Engine control modules (ECMs) are often exposed to temperatures exceeding 125°C.
- Power electronics in electric vehicles can reach even higher temperatures, especially under heavy load or fast charging conditions.
- Brake and transmission systems often experience repeated thermal cycling.
Such high-temperature conditions can affect the reliability, performance, and lifespan of the electronic components, especially the PCBs.
Effects of High Temperature on PCBs
When exposed to heat over long periods, PCBs face several thermal-related challenges:
-
Material Degradation
PCB substrates such as FR-4 tend to degrade at temperatures above 130°C. Prolonged exposure can lead to:
- Delamination of layers
- Loss of mechanical strength
- Electrical insulation failure
-
Solder Joint Fatigue
Temperature fluctuations cause expansion and contraction of materials, leading to stress on solder joints. Over time, this can result in:
- Cracked solder joints
- Open circuits
- Reduced mechanical integrity
-
Thermal Expansion Mismatch
Different PCB materials expand at different rates. A mismatch in Coefficient of Thermal Expansion (CTE) between the substrate, copper traces, and components can cause warping or internal cracking.
-
Reduced Performance of Components
Heat accelerates electromigration and chemical reactions, which can deteriorate performance over time.
Why are special circuit board fabrication techniques needed?
To address the above challenges, automotive PCB manufacturers adopt specific fabrication techniques designed to withstand high-temperature environments. These include:
-
Use of High-Temperature Substrates
Polyimide and PTFE-Based Materials
Unlike standard FR-4, materials like polyimide, PTFE (Teflon), or ceramic-filled composites are preferred for high-temperature applications. These materials offer:
- High thermal stability (Tg above 250°C)
- Excellent electrical insulation
- Low thermal expansion
Tg (Glass Transition Temperature) is a critical parameter that determines the maximum temperature at which the PCB material remains stable without deforming.
Example:
- Rogers RO4000 and Isola P95 are popular high-temp PCB materials used in automotive and aerospace sectors.
-
Heavy Copper PCB Design
High-current automotive circuits often require heavy copper PCBs, which use copper thicknesses of 2 oz or more. This enables:
- Better heat dissipation
- Lower electrical resistance
- Enhanced durability under thermal stress
Thicker copper also supports thermal vias and heat sinks, improving the overall thermal management of the circuit.
-
Thermal Management Techniques
-
Thermal Vias
These are small holes plated with copper that transfer heat from the top layer to the bottom or inner layers, distributing heat away from sensitive areas.
-
Heat Sinks and Heat Spreaders
In power modules and ECUs, external heat sinks are mounted on PCBs to extract heat more effectively.
-
Embedded Copper Coins
Some high-end PCBs embed copper coins directly into the board to enhance thermal conductivity locally, especially near power components.
-
Thermal Vias
-
Advanced Lamination Techniques
Special lamination processes are used to avoid delamination and outgassing at high temperatures. These include:
- Sequential lamination for multilayer PCBs
- Vacuum lamination to remove air pockets
- Use of high-Tg prepregs
These ensure the layers remain firmly bonded even under thermal stress.
-
High-Reliability Surface Finishes
Standard PCB surface finishes like HASL (Hot Air Solder Leveling) may degrade in high temperatures. Alternatives include:
- ENIG (Electroless Nickel Immersion Gold): Good for thermal and chemical stability
- OSP (Organic Solderability Preservatives): Lead-free and heat-resistant
- Immersion Silver or Tin: Used based on application-specific needs
-
Conformal Coating and Encapsulation
To protect PCBs from not only heat but also moisture, dust, and corrosion, conformal coatings like:
- Acrylic
- Polyurethane
- Silicone
- Epoxy
are applied after assembly. These coatings provide thermal insulation, chemical resistance, and electrical protection.
-
Design for Thermal Reliability
PCB layout plays a major role in heat management. Design techniques include:
- Spacing components to allow airflow
- Placing heat-sensitive components away from power sources
- Using copper planes to distribute heat
- Routing power and ground layers effectively
Design for reliability (DfR) principles also emphasizes thermal cycling tests, burn-in tests, and finite element thermal simulations.
Standards and Regulations for Automotive PCBs
Automotive electronics must meet stringent standards to ensure safety and performance in extreme environments. These include:
- AEC-Q100: Qualification standard for integrated circuits
- IPC-6012DA: Automotive addendum to the base PCB performance standard
- ISO 16750: Covers electrical and environmental requirements for road vehicles
These standards emphasize thermal shock, humidity resistance, vibration tolerance, and thermal aging tests.
Applications of High-Temperature Automotive PCBs
High-temperature PCBs are commonly used in:
- Engine Control Units (ECUs)
- Power Electronics for EVs and Hybrids
- ABS and Transmission Control Modules
- LED Lighting Control Systems
- Battery Management Systems (BMS)
As vehicles become more electrified and autonomous, the demand for high-reliability PCBs is expected to grow rapidly.
Trends of Applicable Automotive Circuit Boards
-
Adoption of Ceramic PCBs
Ceramic substrates (e.g., alumina, aluminum nitride) offer superior thermal conductivity and are gaining popularity in power module applications.
-
Flexible and Rigid-Flex PCBs
For space-constrained environments, flexible and rigid-flex PCBs are being used in sensors and dashboard systems.
-
Integration of Thermal Simulation Tools
Thermal simulation during the design phase is becoming common to predict hotspots and optimize layouts before fabrication.
-
Embedded Components
Embedding resistors and capacitors inside PCB layers helps improve thermal performance and reduce board size. See more information about embedded PCBs.
Conclusion
High-temperature environments present serious challenges for automotive electronics. Standard PCBs are not equipped to handle the thermal, mechanical, and chemical stresses encountered under the hood or in high-power applications. As a result, automotive PCBs require special fabrication techniques involving high-temperature substrates, thermal management features, robust design practices, and compliance with rigorous industry standards. With the growth of electric and autonomous vehicles, the focus on thermal reliability and material performance in automotive PCBs will only become more critical in the coming years.
Looking for high-performance automotive PCBs assemblies built to withstand extreme conditions? TechnoTronix specializes in advanced PCB fabrication services tailored for high-temperature automotive applications. From material selection to precise thermal management solutions, we deliver reliable, industry-compliant boards that meet your toughest demands. Reach out [email protected] or request a quote for more information.