5 Effective Ways to Reduce PCB Prototype Spins
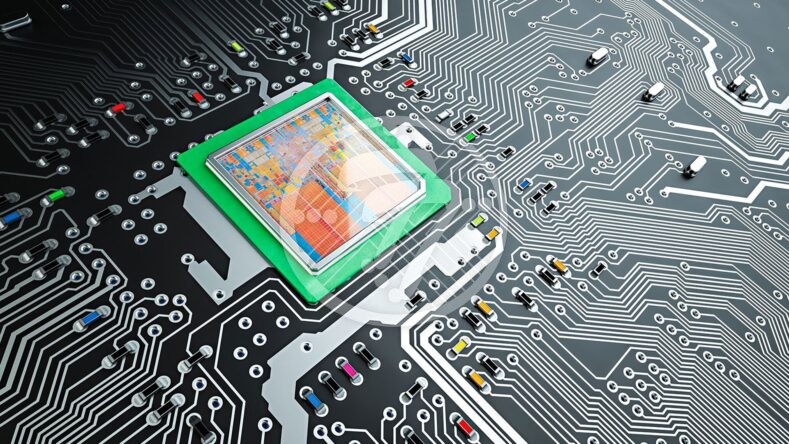
A big mantra of success in the fast paced, ultra-competitive world of today is to be the first to get your product to market without compromising on the quality of the product in terms of either performance or reliability. Getting it right the first time has become imperative in order to garner early mover advantage as also to bring down costs and time associated with manufacturing a product. Each physical PCB prototype has an average cost of $8000, with every PCB prototype spin and re-spin, the costs keep escalating along with delays in manufacturing. Each PCB prototype re-spin involves going back to the design board to correct a design or performance flaw which can derail the entire cost and time estimate for a project. The ability to be the best and first to market your product is limited how well you are able to structure your pcb layout and prototyping process to ensure manufacturability of the PCB at the design phase itself by identifying design issues early on in the design phase itself thereby eliminating the need for PCB prototyping re-spins.
Top 5 Ways to Reduce PCB Prototype Spins:
An optimized design can reduce cost and performance issues during PCB prototyping
It is not uncommon for design engineers to add in more complexity to the pcb layout than required for performance purposes which can sometimes cause issues to manufacturers, particularly if the design component requires a specialized process or machinery which might not be available with the manufacturer. Generally speaking, the fewer the components on the PCB, the greater are its chances of success and it is also less likely to require re-spins due to design issues. Also the lesser the number of components on the PCB the lesser is the time and cost involved which is why PCB specialists emphasize on the importance of optimizing the design for performance required rather than trying to fit in too many components and features which might increase the cost without adding corresponding value to the product.
Knowing your manufacturing partner and his capabilities and processes can help you avoid running into issues later
The best way to reduce the number of PCB prototype spins is to tie in with a PCB fabricator in the early stages of pcb layout itself. A good PCB fabricator can provide you valuable design inputs that can not only help improve the quality and performance of your product but can help you cut down time and cost involved in PCB iterations and re-spins. Each PCB manufacturer or fabricator has his own capabilities and strengths, for instance they can only manufacture PCB’s of specific dimensions or can only manufacture PCB’s of a certain level of complexity. Unless you have taken the time to understand the strengths and limitations of the PCB Partnering with a manufacturer during the design stage itself can help you avoid PCB prototyping re-spins by ensuring your PCB layout conforms to the design specifications required by the PCB Prototype manufacturer.
Ensure a successful Design for Manufacturing (DFM) test before releasing the PCB for fabrication and manufacturing
There is a way to ensure manufacturability before actually running the Gerber files. Partner with your PCB manufacturer to run the design through the DFM tool to ensure the design is error free and manufacturing ready. Verifiability for manufacturing is an important and necessary step that can help you save a lot of time and money on PCB Prototyping re-spins, so ensure you make it an integral part of your process step.
Don’t Skip the Schematic
It can be tempting to skip the schematic if your board is relatively simple, but it’s a bad idea. Building your layout from a complete schematic gives you a reference and helps make sure that all of your layout connections will be complete.The schematic is your visual representation of your circuit. It lets you arrange components near their functional counterparts, regardless of where they will be physically placed. When each pin on each component is depicted in the schematic symbols, a disconnect is easy to recognize. Schematics help you determine if the basic circuit design rules have been followed by visualizing the design.
Optimize budgeted and out of budget costs associated with prototyping by deriving cost to value ratio
Some costs appear big and incurring them might seem a waste of money but can add upto significant savings later. For instance, many organizations prefer working with a small design team to save manpower cost. But in some instances adding 1-2 more people to the team might lead to a quicker design turnaround and reduced PCB prototype spin offs due to greater quality checks resulting in significant savings of time and cost.
Technotronix is an ISO 9001-2015 certified with having RoHS compliance in providing of PCB prototype, PCB assembly and PCB fabrication services to all the dominant industries. Check out our PCB Prototyping services for more information. To get proper consultation or share your requirements to get a perfect PCB with cost effective strategy or to get a quote, drop an email to [email protected] or give a call 714/630-9200