The Complete Guide on PCB Milling in Circuit Board Fabrication!
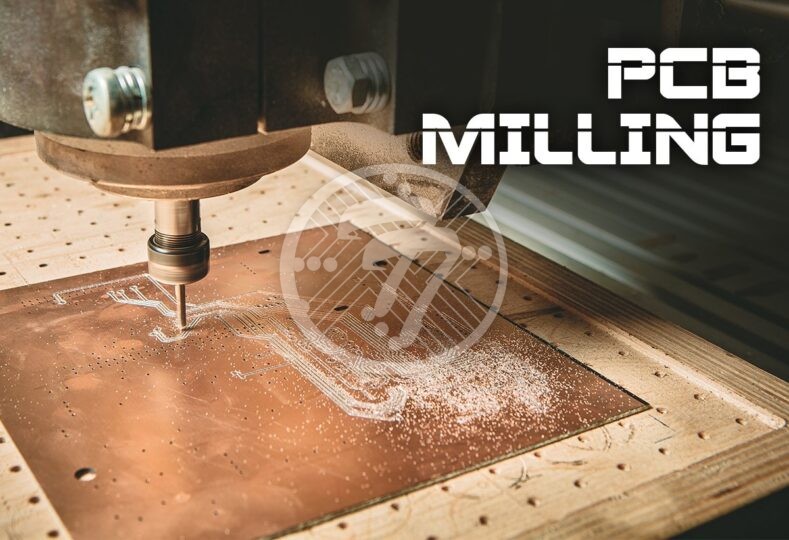
PCB Milling also sometimes referred to as isolation milling or seclusion milling is an important process that is required to ensure high quality PCB boards.
Simply put, PCB milling is an eliminative process that involves the removal of copper tracts from the PCB substance. This ensures that pads are reproduced and configurations established on the PCB design. While milling is similar to etching, in that both are eliminative processes, milling, unlike etching does not involve the use of any harmful chemicals. It is therefore an ideal choice for anyone without a proper lab environment for etching. Also, etching chemicals are usually corrosive and produce harmful fumes when they react with copper traces.
Advantages of PCB Milling
PCB Milling offers a number of advantages when it comes to prototyping as well as some special PCB designs. The biggest advantage, of course, is that it does not involve the use of harmful chemicals. With etching of course not only do you need proper chemical handling but also a proper disposal method in place. The wet process is also unsuitable for high resolution boards.
With a CNC PCB milling machine you can create quick PCB prototypes without worrying about the chemicals. Also the CNC machine can undertake both drilling as well as milling and in some cases also the cutting.
It is important to remember, however, that both milling and etching are preferred under different circumstances. If the requirement is for mass production, for instance, etching is preferred.
PCB Milling Design Parameters
Below is a detailed guide on the design parameters involved in PCB Milling:
- The regular diameter of the PCB mill device is 2 mm while
- the lowest diameter is 0.8 mm.
- The internal or external silhouette of the PCB can be milled as per requirements.
- The borders of the rectangle need to be circular. It is also important that the connected milled area is pierced at every intersection.
- The skeleton and separations of the PCB are milled as in its absence the strength of the PCB board may be impacted. Also, the internal and external silhouette of the PCB board needs to have a layer width of 1 micrometer.
PCB milling process
It essentially involves two systems, namely the hardware and software systems.
Software system
There are two types of software:
- Raster
- Vector
Raster typically does not have high resolving power as compared to Vector.
Hardware system
The hardware system is the numerically controlled milling machine. The system has either a serial or a parallel port that is connected to the main controller. On receiving the signals, the controller drives the positioning system which adjusts the milling head speed.
The movement around the X/Y axis is controlled by stepper motors. The Z-axis drive is also powered by a non-monitored lead screw.
Tips for CNC PCB Milling
Some of the tips to ensure effective printed circuit board milling include:
Leveling
This is crucial as you need to ensure that a uniform level is achieved when subtracting the metal layer off the board. Leveling can be achieved in two ways, physical leveling and computer leveling. Physical Leveling is done using a floating head CNC machine. The milling tool is maintained at a fixed distance from the board. Computer Leveling offers yet another possibility of achieving a uniformly milled PCB. In this leveling, the distance from the board is adjusted through a software.
Track clearance
It is important to pay due attention to the track clearance. Typically a 0.5 mm track clearance is used.
G-Code files
If you are using a machine that can undertake cutting, drilling as well as milling, it is important to have a G-code file for every operation
Coating
It is important to apply a solder mask as once milled the exposed copper can erode.
Safety
When drilling fiberglass you will be subject to dust. It is important that the dust isn’t inhaled. For this purpose, a vacuum cleaner should be used. You can also avoid this issue by using non-dusty FR1 and FR2 copper clad boards.
To sum up
PCB Milling offers a cost effective solution to make strong boards. It is imperative however to follow these tips to ensure that the process is effective.
Technotronix is one of the leading PCB manufacturers based in the USA. We have adopted advanced methods and technologies, which can give you the finest PCB fabrication services. We are adhering to strict high-quality standards and compliant with the RoHS (Restrictions of Hazardous Substance) directives.
If you have questions or queries related to any kind of PCB manufacturing services, email us at [email protected] or call us on 714/630-9200.