What are the key challenges of medical equipment manufacturing? How do the standards and regulations apply to medical device PCB assemblies?
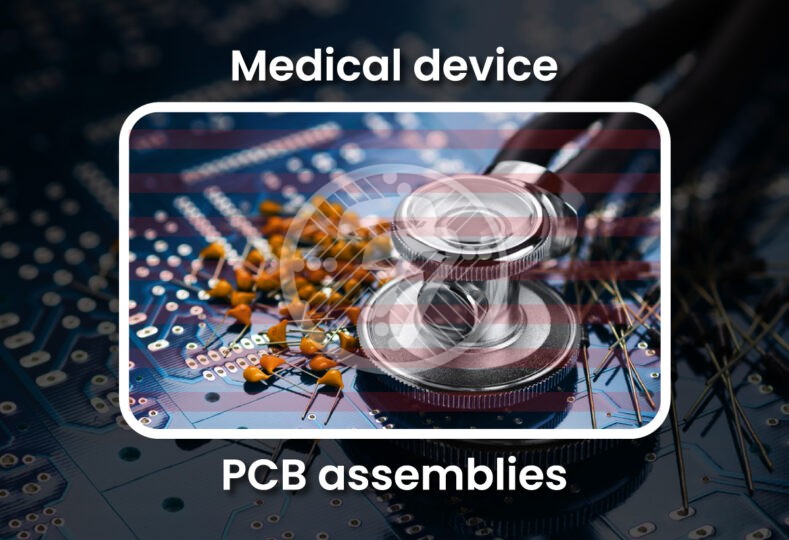
Medical PCBs are the heart of diagnostics and healthcare equipment that undergo rigorous testing to meet industry standards. The growing complexity of modern medicine requires high-quality PCBs that can offer precise, repeatable, and safe operations with a long shelf-life. There are several challenges for medical devices during the PCB design and manufacturing phases. You need to consider factors like consistency, accessibility, and durability while designing medical PCBs. They are expected to be small in size and lightweight as implantable devices. Picking a suitable contract manufacturer who has domain expertise and technical ability is the key to building high-performance medical device PCB assemblies and prototypes.
The healthcare sector needs medical PCBs in applications like monitoring devices, diagnostic equipment, and implantable gadgets. Digitization of health records using computer networks has improved the efficiency and speed of patient care facilities. The software tools assist in patient data consolidation which can be of great value to innovating treatment plans. The tiny implantable sensors and wireless handheld monitors have boosted mobile health support. Miniature medical PCBs are used in devices like BP monitors, pulse oximeters, cochlear implants, etc. Imaging devices like MRIs and CT scans rely on high-quality medical PCBs for diagnosing patient health conditions. Energy-efficient and less invasive medical devices use flexible PCBs to support advanced functionalities.
The PCB manufacturing industry is evolving to accommodate increased signal density and high-speed connectivity of modern medical devices. Recently, IoT technology has been adopted in medical PCBs to facilitate reliable communication in healthcare systems. The challenges for medical PCB development have multiplied with the demand for sophisticated features in the healthcare sector.
Key challenges in building medical PCB devices:
Medical PCB devices are categorized under IPC 610 class 3/3A as they are expected to operate in extreme conditions with consistent performance. Patient safety is the highest concern in this application. So, PCB design and manufacturing have several challenges and as a medical device producer, you have to identify and evaluate the capabilities of contract manufacturers before signing the contract.
Medical PCB assembly challenges:
- The accuracy of signal communication is crucial in medical devices. This depends on many parameters like PCB material, stack up, layout strategy, component selection, etc.
- Medical PCBs have a high mix of analog and digital circuits and hence the design should strictly follow signal integrity guidelines.
- Electro-magnetic interference is a common concern for medical devices. Providing shielding circuits for critical signals is mandatory in medical PCBs.
- Healthcare devices are expected to consume minimal power to run for a longer duration. An optimized power management circuit design is an obvious challenge for PCB assemblers.
Medical PCB manufacturing challenges:
- Validating the production process for the safety and precision of medical devices is a top priority. The process verification ensures adherence to temperature, pressure, and other environmental requirements while manufacturing medical PCBs.
- Maintaining the production cost is difficult as medical PCBs require high-grade substrates and superior components to achieve the expected performance and reliability. Also, additional inspection and testing requirements to meet quality measures increase the overall production cost of medical PCBs.
- Traceability of every part is important in medical PCB manufacturing. Identifying potential manufacturing defects and the ability to backtrack components is essential but difficult.
Standards and regulations for medical PCB devices:
To build quality healthcare devices, the medical industry has outlined some specific standards and regulations. Pick a CM who demonstrates these process compliance and certifications.
The US Food and Drug Administration (FDA) validates the manufacturing and quality control processes of medical device manufacturers. A certified CM assures a quality process that improves product performance and launch timelines.
International Organization for Standardization, commonly known as ISO 9000 outlines the quality and reliability requirements for product design, manufacturing, and testing in all industries. A competent CM essentially obtains and maintains the ISO certification, mostly ISO 9001. Further is an exclusive medical technology standard that defines the documentation process criteria for CMs. This is necessary to track all materials and components used in medical PCB manufacturing. If there are any product recalls, this certification helps your CM to trace back the faulty component source.
IPC-A-600 and IPC-6012 class 3 certified CM can meet the quality and reliability standards for manufacturing medical PCBs. Also, IPC-A-610 describes the acceptability of electronic assemblies.
Medical PCB manufacturing process requirements:
The medical PCB production capabilities and process requirements are quite stringent. The materials used are carefully selected to meet the unique requirements of medical devices. The PCB fabrication and assembly processes need advanced machines to build durable and reliable medical PCBs. Surface mount technology, automated inspection/testing, and trackable documentation are all important requirements for medical PCB manufacturing.
Based on applications like implants, monitors, and diagnostic equipment, the thickness of medical PCB varies. The assembly line should support these varying parameters. Most medical PCBs require RoHS manufacturing setups. A thorough post-assembly cleaning process is compulsory to get rid of any impurities or harmful particles in medical devices.
Medical PCBs are used in critical applications like pacemakers and surgery equipment where data transfer should be highly accurate. Any error in the circuit can have improper consequences on the device operator or user. Thus, medical-grade PCBs should endure rigorous testing before deployment.
Find a certified CM for your medical PCB assembly:
Choose a PCB manufacturer who ensures quality throughout the production process. Testing circuit boards at each step is tedious but crucial for medical PCBs. Though this may increase the cost and delivery timelines, inadequate testing can compromise product safety and usability. To avoid product recalls, your CM should incorporate a robust inspection and test procedure for medical PCB devices.
An expert CM provides supplementary services like design validation, BoM evaluation, and medical industry certifications. They have a well-established sourcing network and can quickly identify component shortages or counterfeit parts in assembly bins. Their domain expertise can assist you in cost-reduction techniques and maximizing production yield. So, work with a CM who is certified in medical technology standards.
Conclusion:
Medical PCB manufacturing involves several challenges as discussed in this article. The importance of precision is paramount in medical PCBs. A tightly regulated process adhering to the medical industry standards can support you in building a successful medical PCB device.