Overcome the Challenges of IOT with Smart PCB Manufacturing
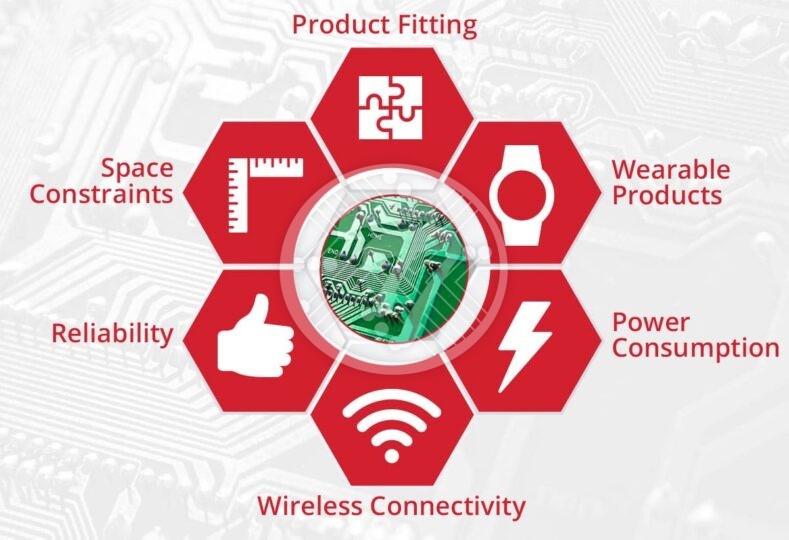
IOT also often known as the fourth Industrial revolution, is not just here to stay, it is only going to get more and more ubiquitous. As per a Gartner research about 26 billion devices are estimated to be connected to the internet by 2020.
All this is not to say that IOT does not come with its own set of challenges. The first and the foremost being, cramming the advanced functionality into shrinking sizes. Check out guide on how modular PCB Design simplifies the complexity for the Internet of Things.
Here is how some of the challenges commonly associated with IOT can be overcome with smart PCB solution:
Space Constraints
When you have to fit the functionality of perhaps a smart phone into the size of a watch, that you have to fight for every inch, is a given. What can help solve this ever-growing space issue is Rigid flex as well as High Density Interconnect PCBs also popularly referred to as HDI PCBs. They allow for dense component placement that saves precious space. Also with rigid flex PCBs, you can fit the smallest of spaces opening up a world of possibilities when it comes to mobile devices. The added advantages that accrue with them include:
- Reduced design limitation
- The possibility of denser circuitry
- Suitability for use in harsh environments
- High tensile strength
- Light weight- in fact they can offer weight savings of up to ninety five percent.
- Greater resistance
- Improved speed and reliability
- Cleaner circuit route- HDI boards offer versatile routing options. Additionally, designers can replace through-holes with microvias, which go a long way in improving signal integrity.
- Cost efficiency- A reduced need for layering lead to a product along with the smaller size also lead to evident advantages in cost.
In fact, Industry leaders focus on combining flex and HDI strategies to create designs that are both appealing as well as offer a whole lot of efficiency. The combination of the two also offers high tensile strength, as also the creation of electronics that are suitable for tough environments. They also go a long way in improving signal quality as well as reducing thermal stress.
Product fitting
Virtual prototyping can go a long way in keeping the design in sync with the IOT form that it is meant for. Often PCB designs would also need to make use of non-traditional materials such as mesh or plastic that will aid functionality.
Wearable products
The thing with wearable tech products is that the PCB design will need to budget for human body temperature, movement as well as moisture. To overcome this challenge smart PCB manufacturing relies on thorough simulation tests. The design needs to accommodate these aspects, as also allow sufficient cooling as soon as possible.
Power consumption
With IOT devices in constant communication with their networks, a strong focus on battery life and power integrity is a must have. The PCB design, therefore, needs to keep energy usage within the individual circuit blocks within a tight budget. Thorough testing can go a long way in overcoming the challenge of high power consumption.
Wireless Connectivity
IOT PCB has the added requirement of providing wireless internet access. This in turn requires installing the right wireless modules and RF Circuit components. Keeping the network speed, power consumption and any security issues in mind will help choose the right components and mitigate the challenges.
Reliability
With IOT devices being used in harsh environments, ensuring reliability and durability is a huge challenge. This can be tackled by using a whole lot of simulation software to test the PCB design under various conditions. In fact it is proper testing as well as working in cohesion with other designers that will ensure that the PCB works reliably under difficult situations.
One of the challenges of IOT is also the transition between the mechanical and the electronic; between the product itself and its PCB form, especially as newer and smaller IOT devices rule the roost. What can come in handy to achieve this is a close collaboration between the designers and engineers through out the design process.
With the industry growing by leaps and bounds, while there is going to be a whole lot of individualization in designs, the fact also is that there will be a lot of common requirements that could allow for some design protocols to emerge. With the development and sophistication in PCB designs the challenges are slowly but surely to get mitigated. The future certainly is one that will be fuelled with technology and innovation- a part that smart PCB manufacturing can play to the hilt. There is no doubt about the fact that approaches to PCB Design will continue to evolve at a rapid pace and that maximizing reliability and reducing errors will be the clarion call for all PCB designers.
At Technotronix, we are fully equipped to handle your PCB manufacturing requirements. With over 4 decades of experience in PCB manufacturing as well as assembling PCBs with differing levels of complexities, we follow industry best practices to ensure we deliver cutting-edge products. Our team of experts and state-of-the-art equipment ensures that all our PCBs meet the industry standards of quality and testing. It is our vast portfolio of satisfied clients that stand as the biggest testimony to our success. In case if you have any questions, please feel free to contact us via email at [email protected]