What’s the difference between Rigid PCB and Flexible PCB?
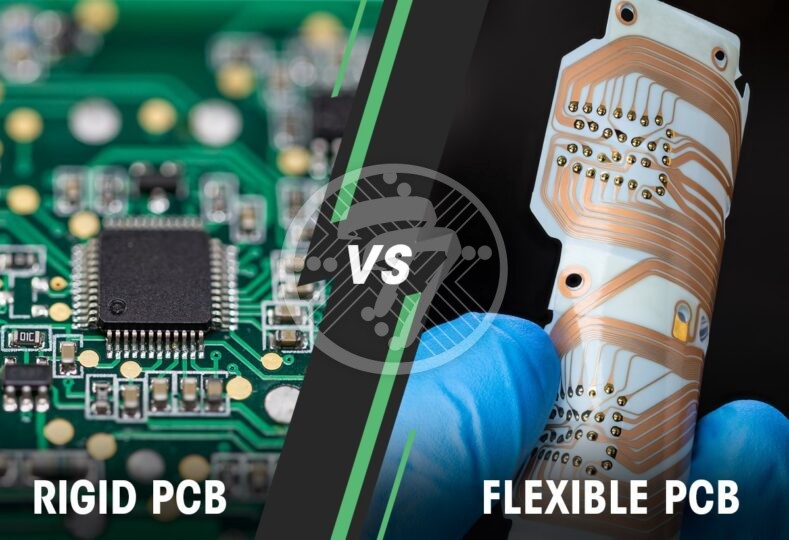
Printed Circuit Board (PCB) forms the core of many electronic devices today. The strength and durability of these devices depend on how strong the PCB is. One can also custom-tailor their PCBs based on the specifications. We have numerous types of PCBs based on their uses and construction like single-layer PCB, double-layer PCB, and multilayer PCB. The other two most commonly used PCBs are rigid and flex PCBs.
In this article, we tell you what are the differences between Rigid and Flex PCBs.
Rigid PCB vs Flexible PCB
As the name itself conveys, rigid PCBs are inflexible while flex PCBs can be bent and shaped to fit on the system in any way.
Flexible PCBs consist of a thin insulating polymer film with conductive circuit patterns and a thin polymer coating for protecting the conductor circuits. Flex PCBs have been used in the manufacture of many advanced electronic products. If designed correctly, flex PCBs are not only versatile but also record no failures. They are of great use in limited space requirements like medical devices, aerospace appliances, automotive applications, and consumer electronics.
Rigid PCBs are also popular owing to their lower cost. In consumer electronics where there is a large space availability, you can use rigid circuit boards. You can rely on the following tenets to understand the differences between rigid PCB and flex PCB.
Design
Rigid PCBs are used in some consumer electronics like desktops, laptops, music keyboards, toys, TVs, etc. If you need more sophisticated designs or meet high-performance standards, your choice should be flex PCBs. Flexible printed circuit boards are also used in low-technology applications like LED lighting and also in bendable applications like kitchen cabinets. Whichever you are using, ensure you are maximizing design and avoid any layout flaws.
Baselayer
The base layer of a PCB tends to be rigid and this contains glass reinforcement. The material used is FR4 that gives excellent stability, mechanical strength, thermal resistance. But the ability to bend is minimal. Flexible circuit base materials are made of polyamide that has excellent flexibility properties but does not have the same mechanical properties as that of rigid PCB materials like FR4.
Copper Layer
Electro Deposited (ED) and Rolled Annealed (RA) are the two types of the copper film. RA is flexible than ED and hence used in flex PCBs. ED is mostly used in rigid PCBs. Of course, it does have certain flexible properties. You can also go for high ductility electro deposited copper used in flex PCBs which is equivalent to RA.
Adhesive Layer
A rigid PCB doesn’t bend and hence the adhesive layer requirements are limited to thermal and chemical properties. The flex PCBs on the other hand has additional requirements that allow bending. The adhesive that is used on rigid board would crack in a flex application. Hence you need to go for something that has stretching properties. For this, make sure to go for an adhesive that has different thermal, mechanical, and chemical properties than the ones used in rigid boards.
Durability
Any electronic device demands high durable designs. Flexible PCBs are more durable because of the low weight of the board. This also reduces the risk of damage caused by high vibrations. Flex PCBs are built using polyamide that makes them well-suitable for extreme heat conditions. If you want your electronic products to bend without any breaking, flexible PCBs are your go-to solutions.
Bend Ratio
Across the route corners of a PCB, electromagnetic interference (EMI) is a possibility and cannot be ignored. You may see it being generated at right angles. If you have chosen a rigid PCB substrate, make sure to have soft corners instead of sharper corners that are often seen in rigid PCBs.
Bend Ratio is the ratio of the thickness of a flex PCB vs the bend radius. If you have chosen a flex PCB, you should think of the bend ratio. Going below the bend ratio results in mechanical failure.
Flex circuit overlay
The manufacturing process of both rigid and flex PCBs is the same. The drilling and plating of holes and vias, photo imaging, etching of copper traces, outlines, and planes, the heating of PCBs for removing moisture are all same. Post this step, rigid PCBs move to the solder mask station and flex circuits go to the circuit overlay station. The difference between circuit overlay and rigid PCB’s solder mask is that the circuit overlay film is flexible.
The film is made of polyimide film coated with a thermoset adhesive that is laminated using pressure and heat for easy flow and to fill in the gaps between pads and traces. This helps in preventing the trapping of air between layers. The adhesive oozes called adhesive squeeze out. Once you finish the lamination process, any component or features cannot be used anymore.
Budget
Usually, rigid printed circuit boards are less costly than flexible PCBs. The rigid circuit boards reduce the weight and size of your design. But that doesn’t mean flex PCBs are too expensive. You can see what you can eliminate in the flex board design to reduce the cost. You can get rid of unnecessary connectors, wire harnesses, etc. So, if you consider this, you may find even the flex PCBs as cost-effective.
Similarities
- Flex PCBs and rigid PCBs are similar in certain aspects.
- End-goal remains the same – connecting components
- Design Standards are similar in terms of hole size and thickness
- Identical manufacturing process
Wind up
Rigid and flex PCBs find their use in different products like rigid PCBs find their way in larger products like TVs, desktops, etc. while flex PCBs are more for compact products like smartphones, and wearable technology. You can choose either of them considering your application’s demands, industry preferences, and impact.
Whether you choose rigid PCB or flex PCB, make sure to follow the rigorous inspection and testing processes to make sure there are no design flaws. Evaluate the PCB types and plan your project milestones. There are manual and automated inspection methods that ease the process of inspection. Make sure you have a fully functional PCB irrespective of what type of PCB you choose.
You can also choose the right Rigid flex PCB manufacturer who can review the PCB layout designs. Check out how Technotronix has been leading the way for over 4 decades in both rigid as well as flex PCBs across multiple industries.