Selective versus Wave Soldering: Which One is Better for PCB Assembly?
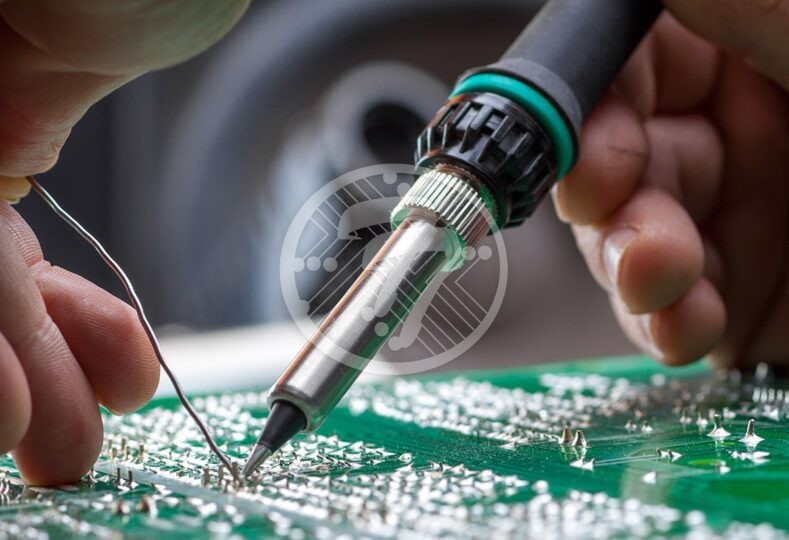
Selective and wave soldering are among the commonly used soldering methods when it comes to Printed circuit boards. Each of these methods however comes with their own set of advantages & disadvantages.
Let’s take a look closure at Selective vs Wave Soldering – Which One is Better for PCB Assembly?
Wave Soldering
Wave soldering, also popularly referred to as flow soldering, this soldering method is undertaken in a protective gas atmosphere as the use of nitrogen is known to considerably reduce possibility of solder defects.
The wave soldering process comprises of:
- Spraying a layer of flux to clean and prepare the components. This is necessary as any impurities can affect the soldering process.
- Preheating of the board. This activates the flux while also ensuring that the board doesn’t suffer from thermal shock.
- Passing of PCB through molten solder. With the PCB moving over the wave, an electrical connection is made between the electronic component leads, the PCB pads as well as the solder.
Wave soldering is extremely beneficial when it comes to volume production, however it comes with its own set of disadvantages, primary among them being:
- The consumption of solder is known to be high
- Similarly it consumes high amount of flux
- Wave soldering is known to use electricity intensively
- It is also known to be high on nitrogen consumption
- Wave soldering necessitates the need of solder rework post he wave soldering
- It also requires that the wave solder aperture pallets as well as the soldered assemblies are cleaned
- Commercially all of this translates into high costs. In fact, the operating costs are seen to be nearly five times as much as selective soldering.
Selective Soldering
Selective soldering is a type of wave soldering used for soldering PCBs that are assembled with through-hole components. With double-sided PCBs becoming increasingly common today as they allow for smaller and lighter products, the usage of selective soldering has also increased exponentially.
Essentially selective soldering comprises of three stages:
- Application of flux to components that need soldering
- Preheating of board
- Fountain of solder used to solder specific components
Selective soldering advantages:
- Process reproducibility
- Process optimization
- Reliability of solder joints
- Since flux is applied locally, it takes off the need to mask certain components
- There is no need for using glue
- It allows for setting different parameters for each component
- There isn’t any need of using expensive aperture wave solder pallets
- It can be used in boards that cannot be wave soldered
- Overall it leads to cost optimization
Additionally Selective Soldering is used when:
- Components are tall and hence they can block the wave from soldering the board
- There is tight spacing of components and hence there isn’t enough place to have a protective fixture around the SMT Assembly parts.
- The boards are thick or have thick copper layers and therefore there is a chance of uneven heating and hence hand soldering is not an option. Selective solder can however use a far-side infrared preheater.
- Dense concentration of through-hole pins do not allow the soldering iron to solder the large number of pins. Selective soldering however allows for use of a wider nozzle which can solder rows of connector pins.
Also as opposed to hand soldering, selective soldering offers the benefit of consistency.
There are, however some disadvantages associated with Selective Soldering as well. These include:
- It requires creating a unique program for each circuit board, which is time consuming and hence the process isn’t particularly suitable for mass production.
- There can be processing errors as there are a host of parameters.
To sum up:
Wave soldering is an ideal method when it comes to Printed Circuit Boards that have through-hole components as well as larger surface mount components. Selective soldering, on the other hand is useful for a densely populated board allowing for a number of parameters to be taken into account. It however is unsuitable for mass production as it requires creation of a unique program for each circuit board.
It is imperative therefore that the soldering partner be chosen dexterously, who can study your distinct requirements and offer the soldering process that fits your bespoke needs. With years of expertise the partner can study the technical requirements as well as ascertain the time & budgets allocated by you to come up with a feasible option.
Technotronix offers PCB Assembly service with 40 years of expertise. Our accurate PCB assembly process meets the quality standards, including ISO 9001:2015, RoHS, and more. Our superior engineering capabilities mean that each board matches your exact requirements and technical specifications. In case if you have any questions, please feel free to contact us via email at [email protected]