Why predictability is essential to save your high-end PCB Manufacturing?
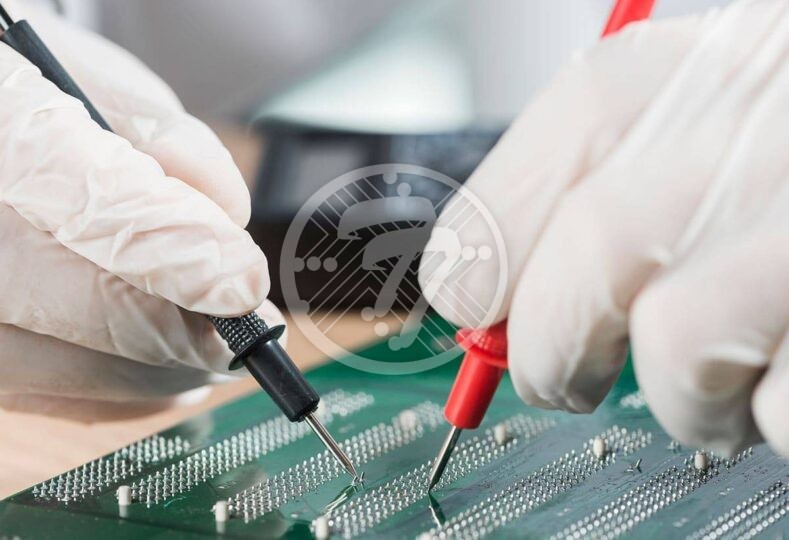
One key way to ensure a product’s reliability is to maintain predictability in its PCB, an essential component of the product. Today, PCBs are integral to almost every electronic device, from phones to computer systems. Industries such as automotive, defense, aeronautics, and technology all rely heavily on PCBs. The ubiquity of PCBs across these sectors highlights the importance of quality PCB assembly services in ensuring consistent performance and reliability.
In all these industries, the reliability of products is of paramount importance. Whether in medical technology or aviation, any mistake can be costly. In the medical field, a device failure can have dire consequences, potentially resulting in loss of life.
This critical need necessitates a new approach to predictability. The traditional reliance on physical inspection in printed circuit board manufacturing is limited, as it only identifies visible flaws. Moreover, physical inspection becomes increasingly challenging with complex PCBs featuring numerous vias, making micro-sectioning and inspection a logistical nightmare. When only a few vias are inspected, the process is never foolproof. With the high diversity of products, traditional statistical tools are inadequate for identifying flaws. Therefore, ensuring predictability in PCB assembly and printed circuit board manufacturing requires advanced, comprehensive methods that go beyond conventional inspection techniques.
The other primary disadvantage with the inspection process is that it can be carried out after the manufacturing process is over. One, this process is costly. Secondly, the flaws could have other inter linkages and thus there is a chance that other lots could also be affected.
For PCBs that are high on complexity and product diversity, therefore, predictability, which traditional inspection cannot guarantee is all the more crucial.
A solution to this issue is the use of extremely comprehensive data analysis, testing automation and digitalization. It is comprehensive statistics that can lead to reliability as well as traceability. With robust data predictions can be accurately made. Any unusual behavior can be called out and atypical products can be removed.
What this essentially requires is that all available data be stored in a centralized manner. In fact each machine needs to be programmed with an interface so that all data is loaded into a centralized warehouse. This in turn, allows in-depth data analysis. It also ensures that unlike the process of physical inspection, relevant correlations are made when there are failures. However even here there is a challenge as data is procured from multiple sources and translates to innumerable data points. This problem can be overcome with formalizing a two-stage data processing format. The first stage refers to normalizing the data and the second, analyzing this normalized data. Scientific data analysis means that you need not rely on finding the issue after the process of manufacturing is over and then respond to it on a reactive basis. Instead it allows you to predict issues on a proactive basis and ensure the chances of failure are minimized. This is made possible as the process input variables are controlled. In turn what it controls are delays which can prove to be extremely costly.
Even though predictability may come at a premium, the fact is that the cost of failure far outweighs this cost.
At Technotronix, we are fully equipped to handle your High – end PCB manufacturing requirements. With over 4 decades of experience in PCB manufacturing as well as assembling PCBs with differing levels of complexities, we follow industry best practices to ensure we deliver cutting-edge products. Our team of experts and state-of-the-art equipment ensures that all our PCBs meet the industry standards of quality and testing. It is our vast portfolio of satisfied clients that stand as the biggest testimony to our success. In case if you have any questions, please feel free to contact us via email at [email protected]