Why Small Batch PCB Assembly should become your preferred method for all kinds of industrial projects?
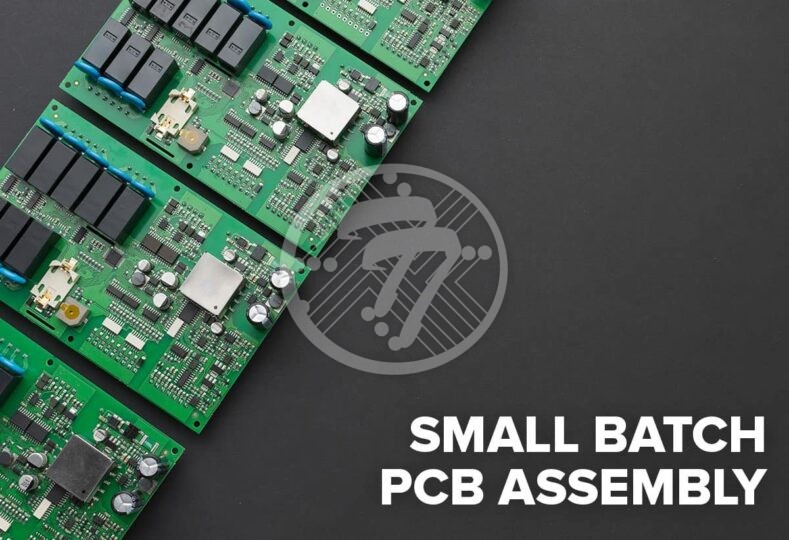
With Printed Circuit Boards becoming an integral part of more and more devices, PCB prototyping is at an all time high. With companies continuously innovating, the need of the hour is small batch PCB Assembly which can offer high turnaround times without the manufacturer being stuck with high inventory that he is unable to make use of.
Advantages of small batch PCB assembly that are of immense value to a manufacturer:
Cost advantage
Although traditionally economies of scale are known to accrue with high volume of production, in an ever-changing technological scenario low volume PCB production comes with significant cost advantages. For one, you will not land up getting more boards produced than you require. Also, with changing technology the boards won’t be rendered redundant.
At the prototype stage, you are often improvising on the product, both in terms of design and functionality. Low batch production means that you aren’t stuck with faulty products. Also, since you are able to outsource PCB small batch. PCB Assembly, what it means in terms of your own business is lower overhead costs. You can also save on precious time that can be utilized in other productive areas of business. With lower batches you also tend to save on storage costs that can accrue in case you are stuck with a heavy inventory load, which is also dead inventory if the prototypes are faulty. Small batch PCB Assembly can therefore offer a low-cost testing method. A Small batch PCB Assembly can therefore offer a low-cost testing method. Check out Top Manufacturing Factors that Affect the Cost of Custom PCB Assembly.
Turnaround time
Low volumes also come with quick turnaround times. You can therefore assess if there are any design changes to e made, quickly. This, in turn leads to shorter time to market, which in today’s world can be a source of significant competitive advantage.
Agility
If there is one attribute that stands between business success and failure, it is agility of businesses to respond to changes. Small batch PCB Assembly inherently offers this advantage to businesses as businesses aren’t stuck with high volume of production as well as have the advantage of quick turnaround times. With improved ability to see whether there are any flaws in the product, whether the design needs any changes, businesses can be extremely agile in dovetailing the product to suit customer needs. Needless to say that the chances of success are increased manifold.
Quality Final Product
With quick turnaround time of PCB prototypes and the ability to detect flaws early, you have the advantage of improving the products and therefore to go to the market with quality products. This goes a long way in improved credibility as the product is successful in the market place and brings repute to the manufacturer.
Feasible for startups and hobbyists as well
Business these days is no longer the realm of large business houses alone. With small batch PCB assembly and the low costs associated with testing out ideas, business has become a level playing field. It is easy for small businesses as well as hobbyists to test their ideas with ease without having to invest large sums of money. For startups wanting to pitch to investors, it is also easy to have a proof of concept beyond just a business plan on paper.
To summarize, PCB small batch comes with multiple advantages, beginning from saving overhead costs by outsourcing your work. Small order sizes automatically lead to improved turnaround times. Also, it is an easy and low-cost way of testing product design ideas without incurring a whole lot of cost.
Technotronix offers professional Custom PCB Assembly with 40 years of expertise. Our accurate PCB assembly process meets the quality standards, including ISO 9001:2015, RoHS, and more. Our superior engineering capabilities mean that each board matches your exact requirements and technical specifications. In case if you have any questions, please feel free to contact us via email at [email protected]