How to Select Most Extensive Surface Finish in the PCB Manufacturing Process?
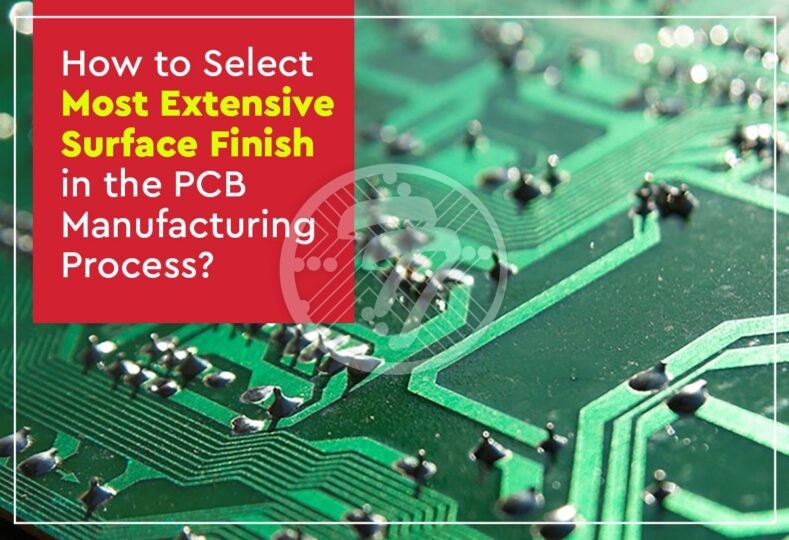
When it comes to electronic assembly, surface finish of the PCB is one of the most crucial decisions that you could take. Surface finish, in turn has implications on a whole lot of issues, including but not limited to:
- Process yield
- Scrap Rate
- Ability to test
- Cost and more.
Selection of the surface finish must be done basis a whole range of factors. Sometimes the mistake that is made, is to go by costs alone. While in the short run you may seem to be saving costs, you could be in for a rude shock in the long term.
The 5 most popular surface finish PCB types:
- Electroless Nickel or Immersion Gold
- Immersion silver
- Immersion Tin
- Organic Solderability Preservative (OSP)
- PB-free HASL
Surface finish PCB comes with their own characteristic advantages to do with:
- Solderability
- Reliability
- Shelf-life
- Fabrication
- Testability
When select surface finish PCB, must consider aspects:
- Do you need direct wire bonding?
- Is corrosion a concern for you?
- Do you need wave solder?
- Is shock or drop a concern area?
- Do you require fine pitch assembly?
- What kind of cost sensitivity do you have?
Let us look at the attributes of some of the surface finishes used in PCB Manufacturing, in some detail:
OSP
This surface finish is typically advisable to use when:
- You need high volumes
- When shock or drop is a concern
- When you are looking for a cost-sensitive product
- Fine pitch components are used.
OSP, however, isn’t recommended in cases where:
- High yield ICT is required
- Wire bonding is needed
Immersion Silver
This surface finish is used by PCB Manufacturers where:
- High yield ICT is required
- Cost sensitivity is important
- Wire bonding is needed
- Shock or drop is a concern area
- Fine pitch components are used.
The limitations of Immersion Silver appear in:
- Where corrosion failure is possible
- Where the cosmetics of the finish are important to your overall scheme of things
Since tarnish is an issue, perception of quality often emerges as an issue with this surface finish.
Immersion Tin
It is recommended to use Immersion Tin Surface Finish in cases when:
- Your requirement is high volume
- You need high yield ICT
- The look and feel of the finish is important to you
- Cost is a concern area
- PB shock is a concern
However, in cases where wire bonding is required or lead-free wave solder is needed it is best not to go in for this surface finish. It is also not a very popular choice with USA based PCB Manufacturer as it comes with a host of environmental and health concerns.
It is recommended to use Electroless Nickel/Immersion Gold Surface Finish where:
The use is this surface finish is rampant where:
- The look and feel of the finish is important
- Wire bonding is needed
- High yield ICT is required
- Fine pitch components are used
- You need a high shelf life
Clearly, however, this surface finish will not fit your bill if:
- You need high volumes
- Shock or drop is a concern area
- You are looking at a low-cost finish
Pb-free HASL
This surface finish is the first choice for PCB Manufacturer California, where:
- Cost sensitivity is a major concern
- Look and feel of the finish is important.
- High yield ICT is required.
In case of high volume requirements or where wire bonding is required, this isn’t a preferred surface finish.
As the above charts reveal, choosing the right finish is a fairly technical task. PCB manufacturers with experience and industry expertise are best suited to choose the right surface finish, which in turn has a lot of implication on the overall success or failure of the electronics assembly. Some of the industries where these finishes typically see a lot of application, include:
OSP
- Computers
- Handheld electronics
Immersion Silver
- Consumer electronics
Immersion Tin
- Aerospace
- Peripheral components
Sometimes, however, the decision of the surface finish is taken erroneously based on:
- The cheapest finish available
- The one that is easily available from the supplier
- The one that allows for testing
- Where field failures are minimum
Each of these approaches can have long-term consequences and need to be avoided in isolation.
Technotronix is one of the leading printed circuit board manufacturer based in the California, USA. We have over 4 decades of experience in providing innovative PCB manufacturing services using modern technologies and latest machinery. We capable to fulfill the varied need of our customer from the simple board to the most complex board for PCB Manufacturing to Assembly and PCB prototype to production.
Know More About Our PCB Manufacturing Service.
For Any Kind of PCB Manufacturing Service, Get A Quick Quote!