Expand the lifetime of your electronic device using flex pcb
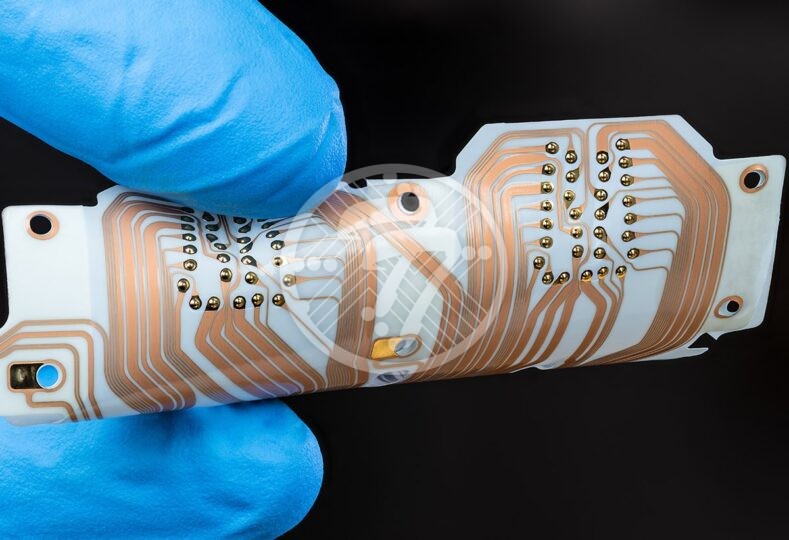
There would be very few takers wanting to build a device to fit the circuit board; most would prefer to design circuitry to fit the device. This is the exact reason why flex and rigid flex circuits are gaining increasing acceptance. They offer multiple advantages both in terms of a new project or even if you want to re-engineer an old one.
Flex PCBs find application in a number of electronic devices, hard disc drives and desktop printers. They are also used extensively in the following industries:
- Communications
- Consumer Electronics
- Automotive
- Medical
- Aerospace
- Military
- Transportation
Even though they are not a new invention, they are increasingly being used for their versatility in design. They are known to unlock both functional advantages as well as cost savings for manufacturers.
Here are some of the key advantages of using flex PCB:
Reliability and increased life span of your electronic device
With both flex and rigid-flex PCB, the number of interconnections required are significantly reduced. What this in turn means is that there are fewer solder joints, contact crimps as well as connectors. Fewer interconnectors means that there are fewer sources of failure and hence greater reliability and increased life span of the device. The flexbility of the circuit also works towards improving shock performance.
flexbility in packaging
A Flexible PCB Board ensures that there is space saving as also more efficient use of space. What this means is that multiple circuit boards, connectors etc. can be replaced with a single unit. Typically it is seen that flex designs occupy 10% of the weight and space occupied by wired solutions. Fewer parts also create less supply chain risk as well as reduced maintenance requirement.
Improved Capability
Flex systems are known for their superior performance. They accept any component or connector that works with a rigid PCB, besides working with direct solders, crimped contacts and the like. Besides, flexble circuits are not impacted by harsh environments, including high temperatures. They are also resistant when it comes to exposure to chemicals, radiations and UV.
Cost Efficient
With lower material requirements, what a flexble circuit board also ensures is lower shipment costs. Also with fewer parts and simple installation the assembly costs are lower. Also with increased reliability comes cost saving on account of longer lasting products.
Also checkout: Flex Printed Circuit Board Cost
Precautions in using Flex PCBs
While a flexble printed circuit comes with a whole lot of advantages, it is important to keep some precautions in mind so that the circuit functions reliably.
There are some features that a rigid PCB can incorporate that a flex PCB must avoid. Primary among them being those that cause discontinuity in the bent areas. A via placed in the bent zone, for example can cause discontinuity. Additionally, conductor width or direction must not be changed in the bent area. An optimum flex-circuit design maintains a uniform width for all conductors. Also, a change in the direction of the conductor in the bend area needs to be avoided.
It is also important not to stack conductors on multiple layer boards. It is also prudent to not have sharp inside corners on the circuit outline as it can cause tears.
Some other areas to pay attention to include the fact that heat should not overstress the circuit. A heat gun can produce high enough temperatures to blister a circuit and hence its use should be avoided. Also, rigid temperature profiles need to be avoided when it comes to reflow flex PCBs.
Wide conductors are known to tolerate bending more than small ones so it is a good idea to widen small conductors in the bend area, even though the widening should be gradual. Also flex circuits with multiple layers are thicker. Often times though the combination of deep plated barrels with the added thickness leads to issues. It is therefore advisable to place vias in areas that have little or no bending or at least in areas that have least amount of bending.
As a standard practice it is also good to place fillets on via pads. They tend to eliminate stress points that have the potential of resulting in cracks.
It is also advisable to consult the Rigid flex PCB manufacturer during the design phase itself as that can lead to finding the most efficient solution that will work for your unique design. With modern software programs complex 3D designs can be accommodated thereby allowing engineers to stack and test flex parts in layers. This in turn reduces the time and costs associated with testing. Modern 3D modeling software helps developers as well as fabricators to align their expectations as also to speed up the entire process.
With the above precautions in place you will be able to use your flex PCB to numerous advantages including giving your electronic products a whole new lease of life.
At Technotronix, we are fully equipped to handle your PCB manufacturing requirements. With over 4 decades of experience in rigid-flex PCB manufacturing as well as assembling PCBs with differing levels of complexities, our team of experts and state-of-the-art equipment ensures that all our PCBs meet the industry standards of quality and testing. In case if you have any questions, please feel free to contact us via email at [email protected].