Top Factors that affect the flex printed circuit board price!
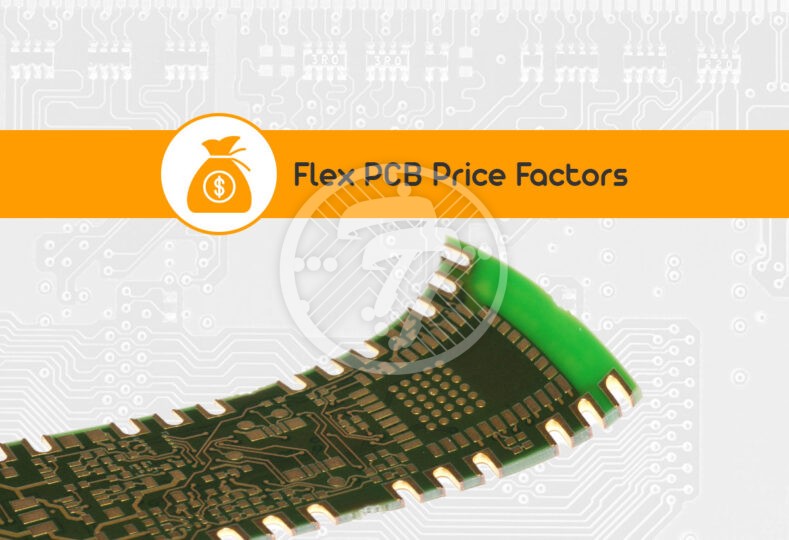
It goes without saying that cost optimization is an important KRA when it comes to designing and manufacturing a PCB. It ensures that the overall project is price competitive and finds acceptability in the market place. What then are some of the cost drivers of flexible PCB board and how can they be controlled. Below is a detailed overview.
Major cost drivers of Flex PCB
The major drivers that impact the cost of Flex PCBs include:
- Circuit Board Material
- Number of Layers
- Size & Shape of PCB
- Spacing & Trace Width
- Copper Foil thickness
- Drill holes
- Drill to copper distance
- Type of Surface Finish
- Type of Stiffeners used
Let us look at each of these Flex PCBs cost drivers in detail:
Circuit Board Materials
Typically, while rigid boards make use of FR-4 material that come at a lower cost, flex boards make use of Polyimide substrate that offer better thermal and electrical properties. In fact, when it comes to the choice of PCB material some of the factors that need to be taken into account include:
- Using a material that offers thermal reliability if the board has to operate in a high temperature environment.
- Ensuring that the material used can withstand physical stress.
- Making sure that the material allows uninterrupted signal propagation.
However, a very important aspect is not to over specify the material requirements. That can significantly drive up your costs. For example, if the PCB does not have to operate in a high temperature environment, you can very well make use of polyester laminate as opposed to polyimide substrate. Similarly simple flex boards can make use of inexpensive materials that work well at lower temperatures.
Number of circuit board layers
As the number of layers in the circuit board increases, so does the cost. This is on account of a whole lot of processing issues such as aligning the layers, ensuring integrity of plated through-holes, issues related to lamination, and more. As a thumb rule, from 4 to 6 layers, there is an overall increase of as much as 30-40 percent.
Size & Shape
Typically, the larger the surface area, the higher the price. Also, PCBs in regular shapes tend to cost less than PCBs in unconventional shapes. With an unconventional shape the panel utilization reduces & the cost tends to go up.
As far as possible therefore, it is prudent to stick to conventional shapes such as square or rectangle.
Spacing & Trace Width
An appropriate PCB trace width ensures that the signals propagate & that there is no overheating. Where spacing is really tight, etching is far more difficult as well as cost intensive.
Copper Foil Thickness
The cost is directly proportional to the thickness of the copper foil. With thick layers the need for high prepregs during lamination, goes up. Whenever there is more than half an ounce of copper on the inner layers and more than 1 ounce on the outer layers, the overall cost tends to increase. Also, thicker copper layers increase the trace width. A word of caution here through – the thickness of copper layers shouldn’t be less than one-fourth of an ounce as that could lead to high processing costs.
Drill Holes
If the drill hole is very small in size, it increases the drilling duration & adds to the cost. It is therefore advisable to stick to standard drill hole sizes.
Drill to Copper Clearance
This refers to the distance of the edge of the drill hole to the nearest copper feature. The smaller this distance, the higher the cost. A typical drill to copper clearance is 8 mils.
Surface Finish
In choosing the right surface finish the product performance as well as the cost need to be kept in mind. There is a wide range of surface finishes that are available. From example ENIG is known for its reliability & the fact that it doesn’t tarnish. It also offers superior solderability but it comes as higher cost than several other finishes. Immersion tin, as a finish, for example is known for its optimum cost and performance though not so much for its durability.
Type of PCB Stiffeners
The importance of stiffeners cannot be overstated. They offer support o components and connectors besides ensuring heat dissipation. Typically, FR4 and polyimide are used. However, aluminum and stainless steel are also sometimes used although they add to the cost.
Also, it is important to remember that stiffeners can either be bonded with a thermally bonding adhesive or a pressure-sensitive adhesive. Thermal bonding adhesive are less expensive than their pressure sensitive counterparts.
Ways to Optimize Costs
While we have looked at the major cost drivers, some of the ways to optimize costs include:
- Limit the number of layers.
- Ensure that the panel utilization is efficient.
- Make sure that the stiffener thickness is uniform.
- Ensure that the number of vias are optimized.
To sum up
It is fairly important that areas for cost-optimization be identified in the design stage itself. Being sure of the choice of material, number of layers, choice of stiffeners, trace width and more, will go a long way in ensuring that the PCB manufacturing process is seamless and that costs are kept under check.
It is also extremely important to make the right choice of PCB contract manufacturer who is equipped with industry best practices to be able to offer optimized cost and a quick turnaround time.
Go with a Technotronix – a professional PCB manufacturer with more than 4 decades of experience and ISO 9001:2015 certified who is equipped with the necessary industry best practices. So, you do not need to undertake unnecessary trial and error beyond a point. Feel free to ask if you have any questions regarding flex circuit boards. Your satisfaction is our primary goal!