Leaded Solder vs Lead Free: The biggest debate in PCB manufacturing!
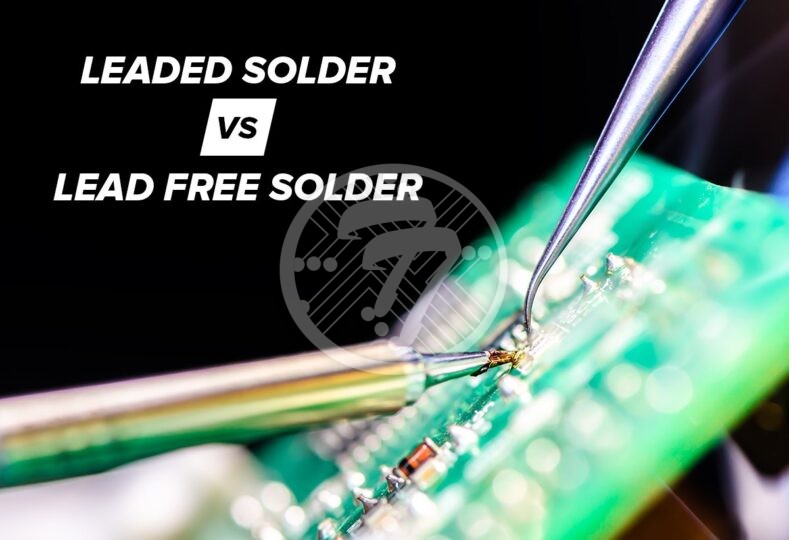
You sure want to stay compliant with RoHS guidelines that restrict the use of hazardous substances in electrical and electronic equipment, lead being one. PCB Manufacturing, however, has been debating the merits of using leaded versus lead free solder for a long time. Let us look at the relative merits of both in detail:
What Are Lead Solders & Lead-free Solders Made of??
Lead solder also referred to as SNPB solder essentially comprises of lead and tin as its base components. Increasingly, the occupational risks of soldering with lead have been highlighted. Essentially, the dust and fumes generated by lead soldering have been found to be toxic when inhaled. Lead based solder is thus a documented health hazard. In 2006, the Restriction of Hazardous Substances Directive (RoHS) was adopted by the European Union (EU).
Lead-free solder has emerged as a replacement of the conventional lead solder. Lead-free solder contains the following substances in varying proportions:
- Copper
- Tin
- Silver
- Nickel
- Zinc
- Bismuth
- Antimony
Some of the commonly used lead free solders include:
1. Tin-Silver
In such solders, the silver acts as a catalyst as also increases the electrical conductivity of the joint. Tin in this case acts as the base metal which offers strength to the solder. It also acts as a protective agent and reduces the possibility of corrosion.
2. Tin-Copper
The role of copper in the solder is to improve mechanical strength as also the electrical conductivity.
3. Tin-Zinc
The use of zinc goes a long way in lowering the melting point of the solder.
Leaded Solder Vs Lead-free Solder Paste
There are several advantages of using lead solder when compared to lead-free solder.
Advantages of using Lead Solder
Strong joint formation
Lead solder typically offers good electrical conductivity between various metals leading to strong joints.
Ease of use
The advantage with leaded solder is that there is no need for any cleaning agents before its application. The solder paste can be applied directly onto the surface. On heating the molten solder flows into the gaps and once it solidifies it forms a strong bond.
Strong Wetting Property
Since lead solder has a strong wetting property, it is easy for it to flow in narrow spaces.
Disadvantage of Using Lead Solder
The disadvantages of using lead solder includes:
Toxicity
On heating, lead solder produces poisonous gases that can pose a serious threat to life.
Heat dissipation
Lead solder is known for its high thermal resistance. This means heat dissipation is an issue.
Flammability
Given the flammability of lead solder, there is high risk of fire.
Cost
Depending upon the purity level of the solder, the cost of lead solder is also high.
Advantages of using Lead-Free Solder
The advantages of using lead-free solder include:
Low cost
Lead-free solder costs lower than leaded solder and is therefore far more affordable.
Environment friendly
The big advantage with lead-free solder is that is does not produce toxic fumes or waste material and therefore does not contaminate the environment.
Safety
With lead free solder being less combustible, the chances of fire are low.
While lead-free solder joints tend to look different in appearance, joints soldered with lead-free solder paste tend to be reliable. Of course, in order to eliminate soldering defects you need to look at many other factors including but not limited to the temperature, vibration, pre-heating time and throughput and the skill level of the operator. The PCB fabricator’s experience in RoHS material compliance can go a long way in ensuring reliability.
The design layout of the circuit board, and the right component selection also have strong roles to play when it comes to quality control issues. Additionally, the choice of lead-free products needs to be made as per the design parameters. Proper board layout and component selection will ensure that there is no damage to electronic components. This is particularly important as during reflow high temperatures are experienced for extended time periods.
To sum up
Reliability of the final product demands that the solder joints are reliable and that they do not act as a heat intermediary. When making the decision of what kind of solder will work best for your PCB manufacturing project, it is important to consider factors such as:
- Safety
- Cost
- Wiring Requirements
- Ease of handling, and more.
With a reliable PCB manufacturer you can rest assured that all RoHS material compliance issues are taken care of without sacrificing quality or time to market.
Technotronix is one of the leading providers of Lead-Free PCB manufacturing services to all the dominant industries. Our main strength lies in the extensive experience and skilled team of experts to build Lead-Free and RoHS Compliant PCB Assembly and manufacturing solution. You can drop an email to [email protected] or give us a call at 714/630-9200 to solve your queries or to get a quote.