Best practices for avoiding solder balls to ensure flawless SMT manufacturing!
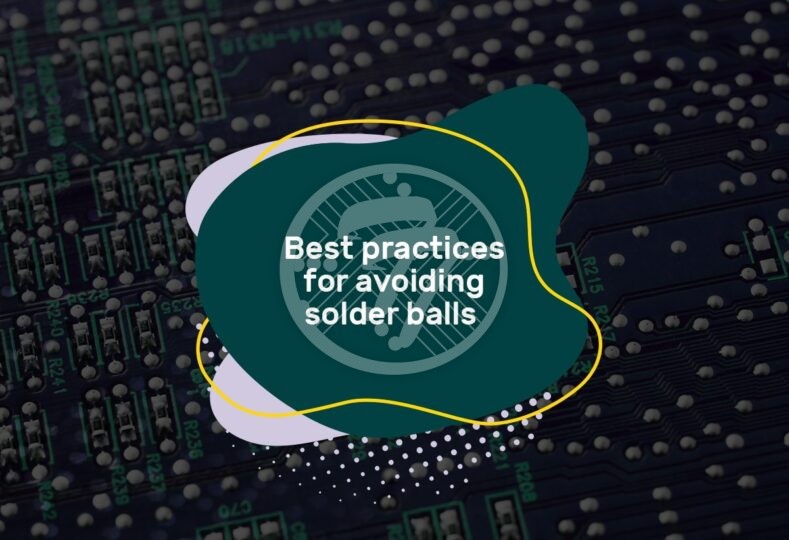
A big issue when it comes to Surface Mount Technology (SMT) manufacturing is the formation of solder balls. These can be caused on account of a wide variety of reasons and can result in several issues even causing the end product to fail. Let us look at what exactly solder balls are and importantly what are the ways to avoid their formation.
What are Solder Balls?
Essentially these are balls of metal alloy that are formed on the surface of the PCB once the soldering process is completed. The formation of solder balls, impact the functionality of the PCB. They can even impact the quality of the component joints especially if they are large in size. Even more damaging is the fact that if these solder balls roll onto other board parts they can cause shorts.
Some of the reasons that lead to the formation of solder balls include:
- High humidity
- Excessive flux in the solder paste
- High temperature or pressure during the reflow process
- Improper cleaning post flow
Top ways to prevent solder balls
Some of the ways to avoid formation of solder balls include:
1. Ensure there isn’t too much moisture
You need to take care that the board is free of moisture. For this, it is important to store the PCB in a dry place. Also it is important to dry the board before production with anti-static cloth. Also, baking the boards at 120 degree Celsius works for four hours works well to ensure that excess moisture evaporates.
2. Choose the right solder paste
Solder paste that is high on metal content has fewer chances for solder balls to form. It is also important to ensure that there isn’t too much flux in the solder paste. While Flux can be used to prevent oxidation however excess of it can lead to a structural collapse.
3. Preheat the PCB
It is important to preheat the boards so that they are as close as possible to the oven’s temperature. This will ensure that the solder melts evenly.
4. Ensure that the solder mask is in place
Ensure that the solder mask is in place and that the solder paste is used properly so that there are no gaps between the traces & the pads. Using high quality equipment as also keeping the rate at which the board is preheated, low are other ways to ensure that the solder spreads evenly.
5. Ensure that PCB mounting stress is under control
If there is a lot of stress on the board when it is mounted, the traces & pads can stretch or condense. If there is too much inward pressure the pads will be pushed closed. On the other hand, if the pressure is too much outwards the pads will be pushed open.
6. Ensure pad spacing is correct
Incorrect pad spacing can lead to issues in solder pooling. Incorrectly placed pads can, not only cause solder balls to form but also for them to fall out & cause shorts. The pads must therefore be placed optimally.
7. Ensure that the stencil is clean
It is important that the excess solder paste is cleaned off the stencil. Any excesses can lead to formation of beads or balls. In fact after each round the stencil should be cleaned. While this may involve time, it will ensure that it does not lead to costly errors.
8. Ensure that the stencil dimensions are correct
It is important to choose a SMT stencil with the right thickness. Stencils that are too thick do not work well. Additionally, stencil opening ratios & shapes need to be paid due attention to.
To sum up
Solder Balls can lead to a wide variety of issues. However, fortunately with some basic precautions you can prevent their formation. It is imperative that you look at your production process step-by-step & ensure that you take the necessary steps so that the formation of solder balls can be prevented. With the above tips you can ensure that the risk of solder ball formation is minimized. It is important that you choose the right electronics contract manufacturer who has the requisite experience and stringent quality control measures to offer high quality PCBs.
At Technotronix, we are fully equipped to handle your PCB manufacturing requirements. We have over 40 years of experience in SMT PCB assembly. Our team of experts and state-of-the-art manufacturing facilities ensure that all our PCBs meet industrial standards. If you are looking for high-quality SMT PCB solutions, you can submit your requirements via PCB SMT assembly quote form. Also, if you have any questions, please feel free to contact us via email at [email protected]