What is the importance of PCB trace width in PCB design?
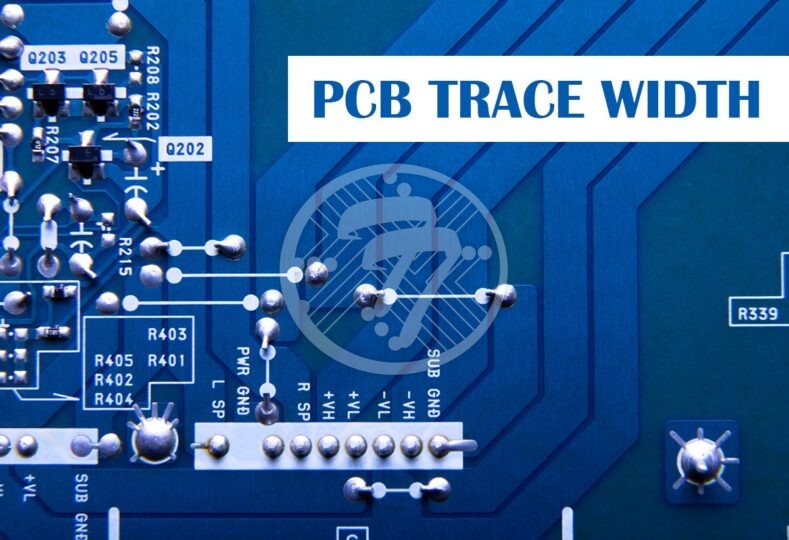
Before we understand the importance of trace widths in PCB board design, let us start with the basics and understand what exactly is a trace width.
Essentially a PCB trace connects electrical signals from one junction to another. The junction can be the pin of a component, an empty pad or test-point. A trace width is measured in mils or thousandth of an inch. Typically, a standard trace width is between 7-12 mil and could be a few inches long.
For boards where there is a specific design requirement such as noise mitigation, speed optimization and more, trace widths and types assume a significant advantage.
PCB fabrication costs are driven up with the following trace-related specifications:
- Trace widths narrower than 5 mils.
- Trace spacing closer than 5 mils.
- Via holes with a diameter smaller than 8 mils.
- Trace thickness thinner or thicker than 1 ounce.
- Differential pairs and controlled lengths or trace impedance.
High-density PCB designs might require trace widths as thin as 2.5 mil. On the other hand, some high-power designs might require very large traces. Designs that call for high-speed communication from one peripheral to another might need traces with controlled impedance. Similarly, high voltage applications need a minimum distance between two exposed differential signals.
Role played by PCB trace widths in layout
Trace widths impact the electrical performance of the printed circuit board, both in terms of:
- Signal Integrity
- Power Integrity
Signal integrity
Using different trace widths can go a long way in improving signal integrity and to keep signal interference, crosstalk, electromagnetic interference etc under control.
Controlled impedance routing
When it comes to certain high-speed signals, they need to be routed at specific widths so that there is impedance control. The trace widths must be correctly figured out based on:
- Dielectric material of the board.
- Spacing to other signals.
- Copper weight.
Microstrip and stripline
In case of sensitive high-speed transmission lines you need to couple them with a reference ground plane so that the traces are shielded. A stripline configuration refers to an internal routing layer that is sandwiched between two ground planes. A microstrip configuration on the other hand refers to traces on the board’s exterior with adjacent plane beneath it.
Analog routing
When it comes to analog signals, they need to be short and direct while having extra width to keep trace impedance low. With analog circuitry, it is also better to minimize the use of vias.
Power integrity
To ensure power integrity it is important to look at the following aspects:
Short and direct routing
It is important to keep the traces short to avoid additional noise. Rounded corners as opposed to right angles are also preferred.
Use wide traces
To reduce inductance and crosstalk it is prudent to use wide traces with power routing.
Current and thermal consideration
Power traces conduct various current levels depending on which net is being routed. Also, it is important to consider the amount of heat the lines generate with the current. The power tracing on the external layers can also benefit from air-cooling.
Using Optimum PCB Trace Width
Several PCB CAD tools can today control multiple trace widths. PCB layout engineers can set up a trace width value. Individual nets, however, can be controlled by specifying the width and the spacing for each. With CAD tools there is also the ability to set up classes of nets. Certain CAD systems also offer the ability to set up different rules for specific areas. When you are routing through dense areas this can be extremely helpful.
Essentially while there are several different ways in which you can set up your PCB CAD system for trace routing, what you need is strong electronics contract manufacturer. You need to ensure that your CM has a strong engineering team, which has the requisite knowledge and experience to be able to set up the PCB CAD systems and design a successful circuit board. The CM should not just understand the nuances of trace widths but also the right usage of tools to ensure that The PCB lives up to the highest standards of quality.
We have over 4 decades of experience in providing innovative high-speed PCB design & manufacturing services. We take an extra step to reach out to your exact PCB manufacturing requirements, high-quality standards, and a strong customer support service to provide quick turnarounds and on-time delivery to our customers. Submit your any custom printed circuit board design service requirements via PCB design quote form along with BOM (Bill of Material) & Gerber files and we will get back to you soon. You can contact us via email at [email protected] or call us on 714/630-9200.