What are the standards for EMI and EMC for PCB design? How to meet them?
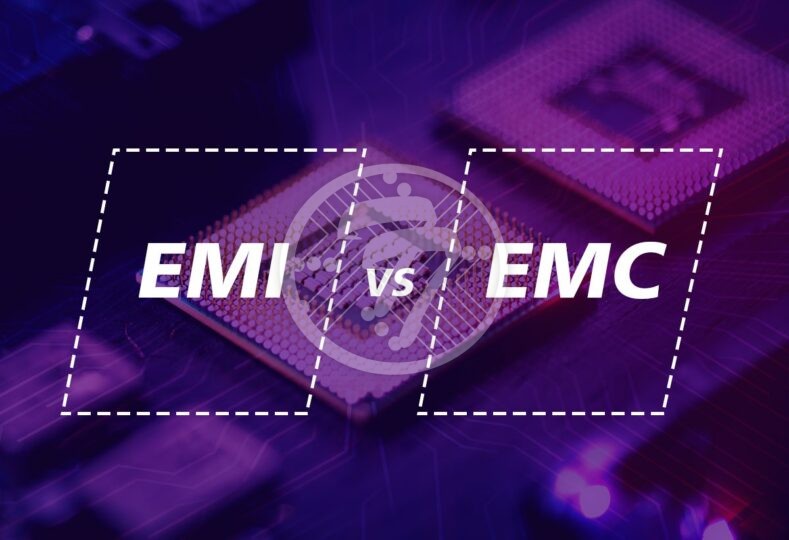
What are EMI and EMC in a PCB?
EMC or Electromagnetic compatibility refers to the ability of the electronic system to operate within an electromagnetic environment without generating EMI or Electromagnetic Interference. EMC ensures that the system performs as intended within defined safety measures.
EMI refers to Electromagnetic Interference or disturbance where when energy is transmitted from one electronic device to another, it corrupts the signal quality and causes malfunctioning of the device.
It is therefore vital to control EMI, a task that can be done in the early stages of the PCB design. In order that your board designing is EMC friendly, a fair amount of importance needs to be given to aspects such as component selection, circuit design as well as PCB layout design. It is when your product passes the necessary EMI/EMC standards that it can be market ready.
EMC/EMI Standards for PCB Design
When it comes to EMC standards there are two broad categories of standards to meet:
- Regulatory Standards
- Industry Standards
Regulatory standards differ from region to region. Early EMC standards were established by the US Federal Communications Commission. The European community, later laid down its own EMC standards which are today known as the EMC Directive.
Industry standards on the other hand as their name suggests are industry-specific. That way they ensure uniformity as well as interoperability. The US Military, for example, has its own set of stringent MIL-STD EMC requirements.
Broad requirements for complying with EMC standards
In order to comply with EMC standards designers, need to look at the following aspects:
- You need to design for EMI immunity. This largely means paying attention to the right stackup & routing strategy.
- The design needs to ensure that the device emits minimum radiation. For his factors such as layer stack, component placement, grounding strategy, and more play a role.
- The device also needs to suppress conducted EMI which can take several forms such as switching noise from SMPS regulators, coupled common-mode noise, and more.
- Fast transients or power fluctuations need to be taken care of. These can appear as voltage dropouts, power spikes or more. Such requirements are particularly applicable on designs with short cables or AC inputs
- In order to comply with EMC standards, the design also needs to withstand surges & ESD.
Here are some effective strategies that help pass the EMC standard tests:
Stackup, Power, and Grounding
If the board is designed with a low inductance ground system, it tends to minimize EMI. In case of multilayer boards placing a ground plane below the signal layers minimizes loop inductance.
It is also a good idea to route signals on an interior layer. Placing traces between two ground planes & then placing the power plane below the bottom-most ground plane is of help. Placing the power plane close to the ground plane ensures capacitive coupling.
Tight coupling needs to be maintained when routing signals from an interior layer to the surface.
Shielding
Careful use of shielding is yet another method of follow. The easiest method to follow is to use grounded shielding that forms a Faraday cage around sensitive components & traces. However this may not be possible in all designs. A grounded via fence around the edge of the board & via stitching on copper pour regions can also offer protection.
Some common types of shielding for suppressing radiated EMI include:
- Shielding Can
- Conductive foam
- Wire mesh material
- Metallic tapes
- Conformal coatings
- Ferrites
Differential Pairs
Use of differential protocols to route the signals where possible is preferable. Differential pairs can produce some EMI & can lead to crosstalk however this is strong only when it is very close to the pair. A differential pair will produce less intense EMI as opposed to a single-ended interconnect.
Mixed-signal Layout and Routing
It works well to separate digital, low frequency analog and RF analog sections of the board. These sections in fact need to have their own dedicated areas in the ground layer. While you need to prevent interference between different board sections you also need to ensure that signals do not have loop inductances.
Bypass/Decoupling Capacitors on the Power Bus
Use of bypass/decoupling capacitors between the power pin of an active component & a grounded via, is advised. This ensures that the residual noise is passed to the ground.
It is important that the right tools as well as the right expertise be available to design PCBs so that they adhere to EMI/EMC standards. The right PCB assembly partner can create a compliant layout as also undertake any rework.
At Technotronix, we are fully equipped to handle your PCB manufacturing requirements. With state-of-the-art equipment, we deliver the highest quality boards that you can rely on. No matter how complex your requirement, you can count on us to deliver to your bespoke needs. If you have any requirements regarding PCB manufacturing or need urgent assistance, contact us at [email protected] or call us on 714/630-9200.