Common mistakes to avoid in PCB layout design for manufacturability!
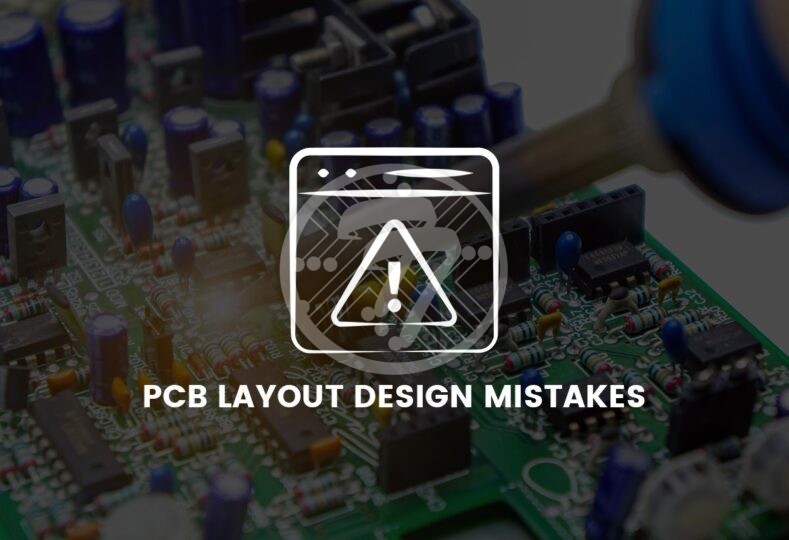
PCB is a crucial component that ensures the functionality of any electronic device. Therefore, optimizing the PCB layout design with the utmost care is essential, as even minor design errors can compromise PCB integrity. Such errors can lead to manufacturing delays and increased costs.
Fortunately, numerous design tools are available to help PCB board manufacturer minimize design-for-assembly errors and reduce costs. By leveraging professional PCB layout services, you can ensure that your design is efficient and manufacturable, avoiding common pitfalls and optimizing overall production.
Here are 7 common PCB layout design mistakes that need to be avoided to ensure that the PCB functions reliably.
#1. Trace Geometry
PCB traces transmit electrical signals between different components of the circuit. The geometry of each trace, therefore, is extremely important. It is important that the width and thickness of each trace be carefully maintained.
It will help to consider facts such as the traces placed on the external layers of the PCB, can carry a higher current at the same thickness as they can take advantage of the heat dissipation. The trace width also depends upon the amount of copper used for that layer. Other than the width, the thickness of each trace also needs to be considered. Several PCB designers often choose a standard thickness value; however, you need to make sure that the thickness value is sufficient for high power tracks. Greater thickness also means a lower resistance to passage of current.
#2. PCB Layout
The importance of an effective PCB layout cannot be overstated. With the trend toward miniaturization, smaller components and reduced distances between them are becoming more common. An inefficient layout can lead to numerous non-compliance issues, particularly when dealing with components that have smaller pitches and higher pin counts.
Choosing a PCB layout design that meets the circuit’s needs is crucial. It’s important to allocate sufficient space on the PCB to accommodate any additional components that may be required. If these components are not used, corrective measures can be taken before PCB manufacturing begins, ensuring a smoother production process and higher overall quality.
#3. Decoupling Capacitors
Decoupling Capacitors have a strong role to play in ensuring that stable power supply is made available to all board components. These capacitors need to be connected in parallel with the power supply. It is also important to ensure that they be placed as close as possible to the pins of the components that need power. The power line also needs to be properly routed to ensure that the decoupling function works well.
#4 Automatic Routing
While many designers tend to take advantage of the automatic routing functionality that is offered by design tools, it is important to remember that automatic routing occupies a large area of the PCB. Besides, it also creates via holes that are larger than what you tend to create with manual routing.
#5. Electromagnetic interference (EMI)
Improper PCB design also often leads to electromagnetic interference. To avoid this, it is important to group elements as per their functionality. For example, there can be different analog and digital blocks, low speed, and high-speed circuits, and more. Additionally, it is important to eliminate right angles on the traces. To reduce interference, it is also important to use metal containers and shielded cables.
#6. Antenna Layout
If the PCB contains antennas to facilitate wireless communication, it is important to ensure that layout errors related to the antenna are avoided.
To maximize power transfer, it is important to adapt the impedance between the transceiver and the antenna. Typically, the transmission line that connects the transceiver with the antenna should have an impedance of 50 Ω. To adjust the impedance accurately, the use of a Pi (LC) tuner filter is ideal. It needs to be placed between the antenna and the receiver.
#7. Blind or Buried Vias
Via holes go a long way in solving complex routing issues. In their use, however, some amount of caution is required.
Blind vias should be used to connect an external layer with an internal one. Buried vias, on the other hand, must be used to connect two internal layers. Through hole vias need to be used to connect two external layers and an internal layer. In creating a via hole, the following things need to be taken in consideration:
- Hole size
- Tolerances, and other attributes.
Also, since blind and buried vias come at a cost, it is also prudent to plan their use judiciously.
Here, in this article we have mentioned some of the most common mistakes that can take place during PCB design process. Make sure to read these guidelines and follow these steps to create a successful PCB design project.
At Technotronix, our broad experience in offering PCB Layout with one or more insulating layers containing signal trace with an exact power and ground for the layout has made us one of the kingpins in providing PCB manufacturing and layout services. Submit your any custom PCB layout and design service requirements via PCB layout quote form along with BOM (Bill of Material) and Gerber files and we will get back to you soon. Alternatively, you can email your requirements at [email protected] or call us at 714/630-9200.